Njta Manual For Traffic Control In Work Zones On Roads

Rest area on northbound at milepost 262 in, A rest area, travel plaza, rest stop, or service area is a public facility, located next to a large thoroughfare such as a,, or at which drivers and passengers can rest, eat, or refuel without exiting onto secondary roads. Other names include, service station, rest and service area ( RSA), resto, service plaza, and service centre.
Manual for Traffic Control in Work Zones. Abstract: This manual is issued by the New Jersey Turnpike Authority (Authority, NJTA) to provide guidelines for temporary traffic control in and through work zones by Authority personnel and by all other entities performing survey, construction or maintenance work on Authority.
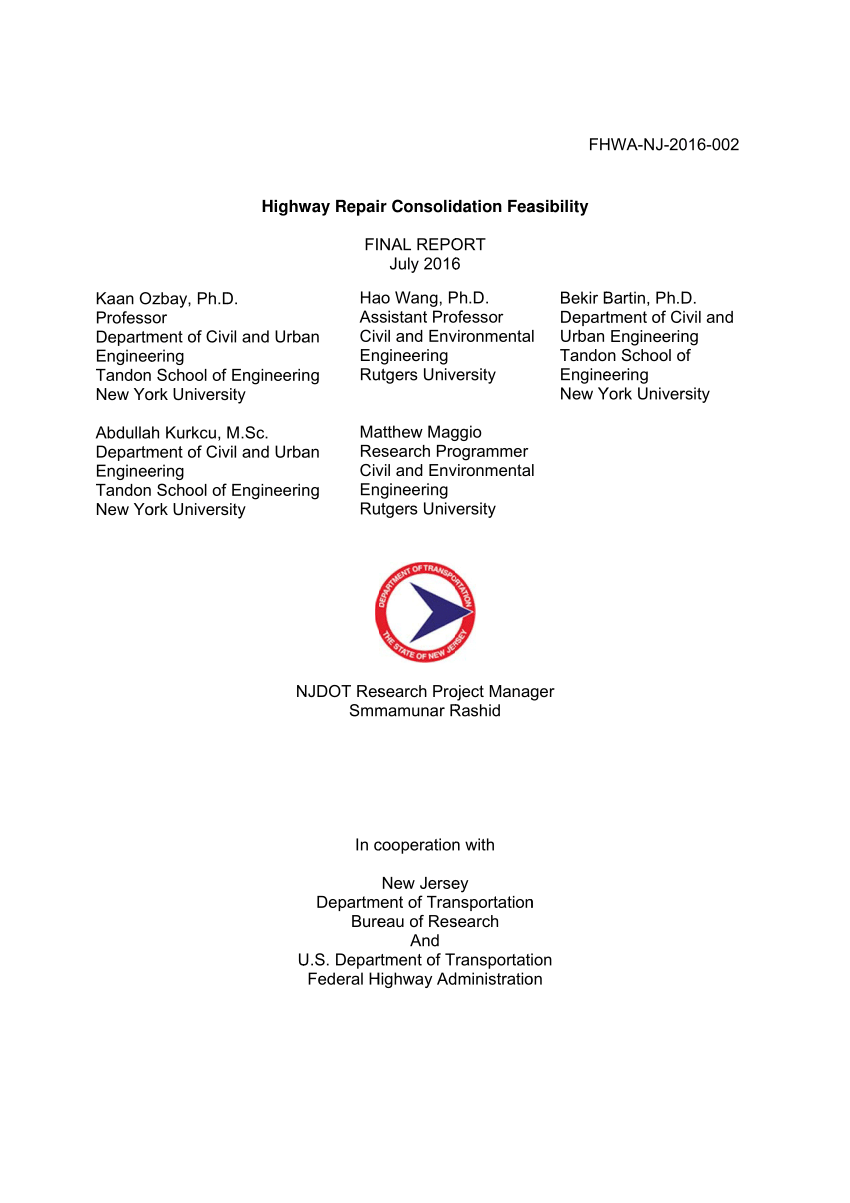
Facilities may include -like areas,,,, and for. A rest area or rest stop with limited or no public facility is a parking area or scenic area. Along some highways and roads are rest stops known as a wayside parks,, or picnic areas. Rest areas are common in the,,, and parts of,, and. The most basic rest areas have no facilities: they consist solely of an exit from the highway that leads to a roadway with paved shoulders, where drivers can rest, look at their maps, or use cell phones.
Contents • • • • • • • • • • • • • • • • • • • • • • • • • • Overview [ ] The standards and upkeep of rest areas facilities vary. Rest areas also have areas allotted for, (big rigs), and. Many government-run rest areas tend to be located in remote and areas where there are practically no or full-service, gas stations, motels, and other traveler services nearby.
The locations of rest areas are usually marked by signs on the highway; for example, a sign may read, 'Next Rest Stop 10 miles' or 'Next Rest Area 25 km'. Driving information is usually available at these locations, such as posted and other local information. Some rest areas have visitor information centers or or stations with staff on duty. There might also be,, pay,, a, a, or a at a rest area.
Some states provide access at their state-owned rest areas or are considering doing so, including California, Florida, Texas & Washington among others. Many rest areas have areas. Rest areas tend to have traveler information in the form of so-called 'exit guides', which often contain very basic maps and advertisements for and.
Privatized commercial rest areas may take a form of a complete with a,, and recreation center, facilities, and,, or all under one roof immediately adjacent to the freeway. Some even offer business services, such as, machines, office, and access. Safety issues [ ] Many rest areas have the reputations of being unsafe with regard to crime, especially at night, since they are situated in remote areas. California's policy is to maintain existing public rest areas, but no longer build new ones due to the cost and difficulty of keeping them safe, although many California rest stops now feature quarters. Some of this reputation may be exaggerated, since the advent of lighting and security cameras in rest stops. Nonetheless, many rest stops continue to warn of theft, and advise those who park to keep doors locked (despite the fact that camping is now disallowed in some rest stops).
North America [ ] United States [ ]. Caltrans rest area on northbound in, 12 miles north of the /I-5 junction In the United States, rest areas are typically non-commercial facilities that provide, at a minimum, parking and restrooms. Some may have information kiosks, vending machines, and picnic areas, but little else, while some have 'dump' facilities, where may empty their sewage holding tanks. They are maintained and funded by the of the. For example, rest areas in are maintained. In 2008, state governments began to close some rest areas as a result of the.
Some places, such as, have laws that explicitly prohibit private retailers from occupying rest stops. A federal statute passed by Congress also prohibits states from allowing private businesses to occupy rest areas along. The relevant clause of 23 § 111 states: The State will not permit automotive service stations or other commercial establishments for serving motor vehicle users to be constructed or located on the of the Interstate System. The original reason for this clause was to protect innumerable small towns whose survival depended upon providing roadside services; because of it, private truck stops and travel plazas have blossomed into a $171 billion industry in the United States. The clause was immediately followed by an exception for facilities constructed prior to January 1, 1960, many of which continue to exist, as explained further below.
Therefore, the standard practice is that private businesses must buy up near existing and build their own facilities to serve travelers. Such facilities often have tall signs that can be seen from several miles away (so that travelers have adequate time to make a decision).
In turn, it is somewhat harder to visit such private facilities, because one has to first exit the freeway and navigate through several intersections to reach a desired business's parking lot, rather than exit directly into a rest area's parking lot. Public rest areas are usually (but not always) positioned so as not to compete with private businesses. Example of blue guide sign indicating services available at next exit, near.
Indicating gas, food, lodging, camping, and attractions at an exit can be found on most freeways in North America. Private businesses are permitted to add their logos to these signs by paying a transportation department (or a subcontractor to a transportation department) a small fee. Until the release of the 2000 edition of the, these signs were only allowed on rural highways. The 2000 MUTCD added provisions for allowing these signs on urban highways as long as adequate sign spacing can be maintained, however, some states (such as California and New York) continue to restrict these signs to rural highways only. Currently, these signs are allowed on urban freeways in 15 states, with Arizona being the most recent state (as of 2013) to repeal the restriction of these signs to rural highways only.
Attempts to remove the federal ban on privatized rest areas have been generally unsuccessful, due to resistance from existing businesses that have already made enormous capital investments in their existing locations. For example, in 2003, President 's federal highway funding reauthorization bill contained a clause allowing states to start experimenting with privatized rest areas on Interstate highways. The clause was fiercely resisted by the (NATSO), which argued that allowing such rest areas would shift revenue to state governments (in the form of lease payments) that would have gone to local governments (in the form of property and sales taxes). NATSO also argued that by destroying private commercial truck stops, the bill would result in an epidemic of drowsy truck drivers, since such stops currently provide about 90% of the parking spaces used by American truck drivers while in transit.
Welcome centers [ ]. Main article: A type of rest area often located near state borders in the United States is sometimes called a. Welcome centers tend to be larger than a regular rest area, and are staffed at peak travel times with one or more employees who advise travelers as to their options.
Some welcome centers contain a small or at least a basic information kiosk about the state. Because air travel has made it possible to enter and leave many states without crossing the state line at ground level, some states, like California, also have official welcome centers inside major cities far from their state borders. In Massachusetts, these rest areas are called tourist information centers and in New Jersey,. Service areas [ ] Prior to the creation of the, many states east of the Rocky Mountains had already started building and operating their own long-distance intercity (turnpikes).
To help recover construction costs, most turnpike operators leased concession space at rest areas to private businesses. In addition, on 'closed' or 'ticket system' toll roads, such as the or the, the use of this sort of service area allows drivers to stop for food and fuel without passing through additional tollbooths and thereby incurring a higher toll., which opened the first such highway in 1940 with the mainline, was the model for many subsequent areas. Instead of operating the service areas themselves, the opted to lease them out to (which was acquired shortly afterwards by the modern-day ), which in turn operated a with a, and franchises as a offering. The turnpike currently leases the gas station space to Pennsylvania-based (which operates instead of garages at the sites) and the rest of the service area space to.
Some turnpikes, such as, were never integrated into the Interstate system and never became subject to the federal ban on private businesses. On turnpikes that did become Interstates, all privatized rest areas in operation prior to January 1, 1960 were. Such facilities are often called service areas by the public and in, but each state varies. View from 'Scenic Overlook' near. Text stops [ ] In 2013, the state of New York launched 'It Can Wait', a program for encouraging drivers to pause at rest stops and parking areas along state roads to (thereby avoiding ) by designating all such areas as 'text stops'. The practice involves placing road signs which indicate the nearest 'texting zone' at which to legally stop and use mobile devices such as. Other types [ ] Rest areas without modern restrooms are called ' waysides'.
These locations have parking spaces for trucks and cars, or for only. Some have and.
In Missouri these locations are called ' Roadside Parks' or ' Roadside Tables'. A scenic area is similar to a parking area, but is provided to the traveler in a place of natural beauty. These are also called. Canada [ ] Most of the service centres in Canada are situated in the provinces of and, along their and networks. De Lucht Rest Area on the Dutch A2 Both the frequency and quality of European rest areas differ from country to country. In some countries such as Spain rest areas are uncommon – motorists are directed to establishments that serve both the travelling public and the local population; in other countries access to a rest area is impossible, other than from a motorway. The Dutch rest area is typical of many European rest areas, in that it has no access roads other than from the motorway itself.
Finland [ ] Rest areas are constructed and maintained by the national government, but the local municipality provides local maps and sanitary services. If there are commercial services, the shop has the responsibility for cleanliness of the area. Rest areas are designed mostly for long-distance voyagers. The recommendation is that there should be a rest area each 20 km (12.4 mi).
France [ ] In France, both full service areas and picnic sites are provided on the network and regulations dictate that there is one such area every 20 (12.4 ) on autoroutes. Both types may also be found on national (N-class) highways, although less frequently than on autoroutes. They are known as aires, specifically aire de service and aire de pique-nique respectively, while aire de repos ('rest area') usually refers to a picnic stop. These types are not usually stated on approach signs, but are instead distinguished by the symbols used. A name is usually given, generally that of a nearby town or village, such as ' aire de Garonne'. Main article: The term 'rest area' is not generally used in the United Kingdom.
The most common terms are motorway service areas (MSA), motorway service stations, or simply motorway services. As with the rest of the world, these are places where drivers can leave a motorway to refuel, rest, or get refreshments. Most service stations accommodate fast food outlets, restaurants, small food outlets such as and coffee shops such as; many service stations also incorporate motels such as. Almost all the MSA sites in the UK are owned by the and let on 50-year leases to private operating companies. However, in December 2008, after a change in the law, the only current official 'rest area' in the UK was created at, on the newly opened section of the M6 between Carlisle and the Scottish border. Small, basic lay-by on the UK's, north of Yoxford.
Lay-bys [ ] The term lay-by is used in the and to describe a roadside parking or rest area for drivers. Equivalent terms in the United States are 'turnout' or 'pullout'. Lay-bys can vary in size from a simple parking bay alongside the carriageway sufficient for one or two cars only, to substantial areas that are separated from the carriageway by verges and can accommodate dozens of vehicles. Lay-bys do not appear on in the UK, where until recently only full were permitted. On other roads, they are marked by a rectangular blue sign bearing a white letter P, and there should also be advance warning of lay-bys to give drivers time to slow down safely. In practice, many local authorities neglect to maintain these signs to an adequate degree, and sometimes they are missing entirely.
[ ] Lay-bys are generally beneficial to, as they provide somewhere safe for drivers to stop, whether they wish simply to rest, check directions, make a phone call (as it is illegal to use a mobile in the United Kingdom except in an emergency – ), stretch their legs, or get refreshments, or if their car has broken down. At some larger lay-bys mobile catering is provided by vendors operating from converted,,. These facilities generally offer much better value for money than roadside restaurants and therefore tend to be popular with. Some lay-bys have parking restrictions to prevent using them as overnight parking, or as a long term storage area for trailers, and some have been permanently closed off by councils because of problems caused by their occupation by or other itinerants. Honshū-Shikoku contact bridge, a rest station at in Japan. In,,,, and, rest areas have ( musola) for travelling more than 90 kilometres (56 mi) (2 marhalah; 1 marhalah ≈ 45 kilometres (28 mi)).
In Iran it is called Esterāhatgāh (:استراحتگاه) meaning the rest area or rest place. In Malaysia, an (OBR), or overhead restaurant, is a special rest area with above the expressway. Unlike typical laybys and RSAs, which are only accessible in one-way direction only, an overhead restaurant is accessible from both directions of the expressway. In, there are two grades of rest areas on. These are part of the tollway system, allowing a person to stop without exiting the tollway, as exiting and reentering the tollway would lead to a higher overall toll for the trip. They are modeled and named after the 'Motorway Services' offered in Britain.
The larger rest area is called a ', or an SA. SAs are usually very large facilities with parking for hundreds of cars and many busses - offering toilets, smoking areas, convenience stores, pet relief areas, restaurants, regional souvenir shops, a gas station, and sometimes even tourist attractions, such as a ferris wheel or a view of a famous location.
They are usually spaced about one hour apart on the system, and often a planned stop for tour buses. Two Service Areas also have a motel.
The other grade of rest stop is a 'Parking Area', or a PA. PAs are much smaller, and spaced roughly 20 minutes apart on the system.
Besides a small parking lot, toilets and drink vending machines are the only consistent amenities offered, while some larger parking areas have small shops, local goods, and occasionally a gas station - but are much smaller than their larger Service Area counterparts. The precursor to the tollway rest areas were public and private ' along almost any trunk road - places to rest, eat, and shop for local goods on the traditional road system. Popular rural roads that lead to remote tourist locations still have popular road stations, but with the rise of the tollway system, previously popular routes have been bypassed, leading to the decline or closure to once popular road stations all over Japan. In Korea, a rest area usually includes a park and sells regional specialties.
Cellphone charging is free and WiFi is available in every rest area. In Thailand, bus travel is common, and long-distance bus rides typically include stops at rest areas designed for bus passengers. These rest stops typically have a cheap noodle or curry restaurant as well as a small store for buying food.
Australia [ ]. Roadside 'rest area' 20 kilometres (12 mi) north of Rest areas in Australia are a common feature of the in rural areas.
They are the responsibility of a variety of authorities, such as a state transport or main roads bureau, or a local government's works department. Facilities and standards vary widely and unpredictably: a well-appointed rest area will have bins to deposit small items of litter, a picnic table with seating, a cold water tap (sometimes fed by a ), barbecue fireplace (sometimes gas or electric), toilets, and – less commonly – showers. Other rest areas, especially in more remote locations, may lack some or even all of these facilities: in, a rest area may be no more than a cleared section besides the road with a sign indicating its purpose. Rest areas in Australia do not provide or restaurants (such facilities would be called or ), although there may be, often run by, providing refreshments to travellers.
Comfort and hygiene are important considerations for the responsible authorities, as such remote sites can be very expensive to clean and maintain, and vandalism is common. Also, Australia's dependence on road transport by heavy vehicles can lead to competition between the amenity needs of recreational travelers and those of the drivers of heavy vehicles — so much so that on arterial routes it is common to see rest areas specifically signed to segregate the two user groups entirely. Thus rest areas generally do not allow overnight occupation.
In, however, well-maintained rest areas sometimes explicitly invite travelers to stay overnight, as a road safety measure, but this is rare elsewhere. See also [ ] Wikimedia Commons has media related to.
• • • • References [ ]. • Reed, Aaron (January 18, 2008)..
Retrieved June 7, 2011. Streets and Highways Code Sections 225.5 and 731. • such as those in Missouri rest areas •. Consumer Reports. Retrieved 2010-07-25.
Retrieved 2010-07-25. • Gordon Dickson, 'Government Work Zone,' Fort Worth Star-Telegram, 4 August 2003, sec. • Thomas Corsi, Robert Windle, A.
Michael Knemeyer, 'Evaluating the Potential Impact of Interstate Highway Rights-of-Way Commercialization on Economic Activity at Interchanges,' Transportation Journal, vol. 2 (Winter 1999): 16-25. • Anonymous, 'NATSO denounces pro-commercialization in highway bill,' National Petroleum News 95, no. 5, (May 2003): 9. Massachusetts Department of Transportation. Retrieved 2011-09-16.
Archived from on December 13, 2007. Retrieved 2009-07-16. • February 10, 2008, at the. Retrieved 2009-07-16.
Retrieved 2009-07-16. Retrieved 2009-07-16. • • August 27, 2006, at the. Retrieved 2009-07-16. • Press release (September 23, 2013)..
Office of the Governor of New York. Retrieved 2009-07-16. • • ^ Alberta Official Road Map (Map) (2011 ed.). Alberta Tourism, Parks and Recreation. access-date= requires url= () • ^ (PDF).
Alberta Transportation. Retrieved 2011-03-23. Valuation Ovvice Agency. Retrieved 12 July 2013. Allow rear access to the site to be used other than by MSA staff, delivery vehicles, and the emergency services • • ^. Retrieved 2010-01-25.
Retrieved 2010-01-25. Retrieved 2010-01-25. • Lay-by and advance warning of lay-by signage from the. • Advance signage of lay-bys instructions in, sections 4.8 and 4.9, from the. External links [ ] Look up or in Wiktionary, the free dictionary.
• • • • • Examples of rest area locations [ ] • • • •.
Funded by the Renew Atlanta Infrastructure Bond, the North Avenue Smart Corridor project is using the latest technology to increase safety and improve multimodal traffic operations in this 2.3-mile stretch of roadway. In a partnership with the Georgia Institute of Technology and the Georgia Department of Transportation, data is gathered and analyzed to assist both short- and long-term transportation planning to create a safer and more efficient place to live, work, and play. North Avenue connects some of Atlanta’s most important destinations, institutions and companies, including Coca-Cola headquarters, AT&T headquarters, Georgia Institute of Technology, Georgia Department of Transportation, the MARTA North Avenue Station, Ponce City Market, and the Atlanta Beltline.
We worked collaboratively to discover and deliver innovative technologies including: •Installation and use of hundreds of internet of things (IoT) sensors at 26 signalized intersections •Urban environment adaptive signal timing system •Vehicle-to-infrastructure communications •Bluetooth travel time and origin destination system •Demonstrating connected automated vehicles •Reconfiguration of existing roadway through restriping to support crash reduction and accept autonomous vehicles The adaptive system technology deployed combines artificial intelligence with traffic theory. The system is designed for urban network traffic flows including pedestrians, bicyclists, and transit. It responds to real-time events on demand for all mobility types through advanced video detection systems with built-in analytics that detect vehicle types, speed, volumes, queues, and traffic data statistics. The communication from the infrastructure and different mobility users is disseminated to a smart phone app “Travel Safely.” Cyclists and pedestrians are alerted of vehicles approaching too fast or too close to them, drivers receive signal timing data to their phones and cars, and drivers are alerted when they are speeding through a school zone or sharp curve.
The “everything connected to everything” concept connects all mobility users to each other and to the infrastructure in the street. The technology also increases safety by prioritizing fire engines and ambulances traveling through the corridor for faster emergency response times. Roadway striping was reconfigured to reduce crashes and support the future acceptance of autonomous vehicles. Pedestrians no longer rely on a push-button crosswalk because of combination thermal imaging and video cameras that provide pedestrian and bicycle detection for adaptive control of the traffic signals, Hawk systems, and rectangular rapid flashing beacon systems. The next phase of deployment on North Avenue includes automated vehicle shuttles with transit priority that are connected to the smart infrastructure. North Avenue is serving as a public demonstration and “living lab” for IoT deployment. It is a model of data collection and analytics, connected and autonomous vehicles, and unique partnerships.
It fundamentally transforms how the City of Atlanta plans for, designs, and operates its transportation infrastructure going forward. The expertise and performance on this project has elevated the City’s profile as a leader in transportation innovation.
North Avenue Smart Corridor project was selected as a State Award winner for the in the “Building/Technology Systems” category. The Intelligent Transportation Society of Georgia awarded North Avenue as the. “Around a fifth of disabled people report having difficulties related to their impairment or disability in ”. Atkins is part of a seven-partner consortium who are developing a digital platform that is setting out to improve the rail travel experience for disabled passengers in the UK. The Rail Safety Standards Board (RSSB) co-funded programme will facilitate the sharing of disabled customers’ travel requirements with train operating companies (TOCs) and other service providers. TOC Ability aims to enhance passenger experience and has the potential to transform the experience of those users that need it most. Through the creation of a collaborative ‘intelligent accessibility hub’.
This digitally-led solution seeks to enable the rail industry to measure and maximise the impact of improvements to customer accessibility, exchanging real-time data about rail journeys between disabled customers and train station staff. Atkins’ intelligent mobility team is providing project management, functional design and business modelling expertise to support the development and implementation of the new system. By sharing increasingly accurate journey information in real-time between staff and customers, TOC Ability promises to make journeys more seamless and reliable, reducing passenger anxiety and stress and enhancing comfort.
The resulting increase in trust in the service is expected to encourage more customers with accessibility needs to travel by rail., Director for intelligent mobility and also chairman to an international charity for people with disabilities, says: “TOC Ability is set to transform future rail services for disabled passengers, who are often the most vulnerable, so they feel confident to travel. By improving ways that passengers and operators communicate and interact, we aim to provide an efficient and improved service experience. TOC Ability is a fundamentally important project for the sector, and very much in line with our vision to put the user at the centre of transportation.' The project, valued at around £1.4 million, will run for a period of 18 months. Allowing the consortium to scope, develop and pilot the TOC Ability platform. Testing, in a live train station environment across London, will start in Summer 2018, with the project’s Accessibility Panel, a group of people with varying accessibility needs.
TOC Ability will also be designed to meet international governance standards for data protection, including compliance with the EU’s General Data Protection Regulation Act in respect of sharing sensitive customer data. Atkins is working in collaboration with industry and academic partners as part of the TOC Ability consortium that includes Transport for London, Arriva UK Trains, Goss Consultancy, Enable iD, University of Surrey and Loughborough University. The project’s Industry Advisory Group also includes Network Rail, The Rail Delivery Group, and Office of Rail and Road (ORR), and provides insight and input on strategic direction for the future of rail travel in the UK., Atkins' technical director, said: “TOC Ability has the potential to transform the experience of rail passengers that need it most. By sharing relevant information in real-time between staff and passengers, it promises to make journeys more seamless and reliable, reducing passenger anxiety and stress and enhancing comfort. By increasing accessibility and trust in rail services we are looking to encourage more disabled passengers to make regular journeys and to feel that they are an integral part of our mobility system.” For more information visit the iM Hub:.
Though the region has seen an active military presence since the 1940s, there is no nearby national veterans’ cemetery to serve the burial needs of the many thousands of active duty and retired veterans who call the area home. The closest national cemetery is located at Ft.
Logan in Denver, which is approaching capacity and has a limited projected life. That will change with the construction of the Pikes Peak National Cemetery, which is expected to serve more than 95,000 veterans, their spouses, and eligible children for the next 100 years. Atkins, along with prime architect AES Group, provided comprehensive design services for the new, 374-acre cemetery in the southern portion of Colorado Springs. The initial 65-acre phase will feature 13,000 gravesites and accommodate both casketed and cremated remains.
In addition to gravesites, the cemetery will include the following features: • Main entrance area • Administration building • Maintenance building • Honor guard building • Flag pole assembly area • Memorial walkway • Committal shelters • Public information center with electronic gravesite locator • Infrastructure features such as roads, landscaping, utilities, and irrigation Green building principles and renewable energy initiatives are being incorporated, and the completed Phase 1 of the project will be LEED silver certified and will meet all federal energy and sustainability mandates. To protect future development of the cemetery, Atkins is also providing channel stabilization and restoration along the Corral Tributary to prevent erosion. Atkins prepared the plans, specifications, and estimates for the rehabilitation and replacement of expansion joints and hinges, and deck repair for the 11 bridges that comprise the second-level roadway. This project covered 2.6 miles of bridge structures and more than 650,000 square feet of surface area.
The rehabilitation consisted of repairing the 49 expansion joints and application of polyester concrete overlay. Expansion joint repair included bearing pad replacement, expansion joint seal replacement, and hinge seat repair. Polyester concrete overlay was applied to protect high steel already exposed and to correct drainage.
Because LAX is one of the busiest airports in the nation, Atkins recognized the importance of efficient traffic control planning. In addition to coordinating with various stakeholders to maintain adequate levels of service, special attention had to be paid to timing lane closures and detours optimally to produce favorable traffic patterns. Atkins coordinated with numerous stakeholders, including landside operations, ground transportation, parking operations, LAX police, emergency services, and the airlines, to successfully develop traffic control, lane closure, and detour schemes for each construction phase to ensure minimal traffic delay. Engineering News-Record California awarded the project its -Airport/Transit Category. The project included converting existing domestic gates into eight new international gates capable of supporting wide body aircraft. As a subconsultant to the prime architect, Atkins provided gate planning services for the airport parking layout, and civil engineering services for a new sterile corridor which directs passengers from the converted gates at the airport’s Satellite D into an underground tunnel connected to existing international infrastructure at Terminal 3.
The major civil construction items include pavement removal and replacement for the tunnel construction and 15 additional fuel pits required at D Gates, excavation and backfill for the tunnel, utility line relocations, and a new contaminated drainage system including oil water separator and related structures. The gate planning effort was a momentous challenge as the project’s success hinged on being able to park the Airbus A380, the largest passenger aircraft in the world, at gates originally intended for aircraft one-third its size. The Atkins Aviation Planning team conducted a robust gate planning analysis of the airport’s gates D-19 through D-26, to convert them from domestic, narrow body aircraft operations to international, wide body aircraft operations. The approach maximized the potential for wide body gate utilization, enabling the airport to accommodate an A380 with a dual jet bridge configuration; one for each aircraft deck. Engineering News-Record Southwest Region awarded the project its -Aviation/Transit Category.
Historically, water would flow slowly through this iconic “river of grass” from Lake Okeechobee, one of the biggest freshwater lakes in the country, through freshwater swamps, sloughs, and tree islands into the estuarine areas of Biscayne Bay, Florida Bay, and the southwest Florida coast. Beginning in the 1800s, however, water was diverted from its natural flow into and through the Everglades for flood control, agricultural, and habitation purposes. By the mid-20th century, about 50 percent of the Everglades were lost, destroying the area’s ecosystem while potentially diminishing freshwater supplies for nearby residents through saltwater intrusion. The Comprehensive Everglades Restoration Plan (CERP), approved by the U.S. Congress in 2000, is a 30-year, $12 billion ecosystem restoration plan that hopes to achieve sustainability for the natural system in south Florida. Headed by the U.S.
Army Corp of Engineers and its non-federal lead sponsor, the South Florida Water Management District, the overall program involves, as much as possible, restoring habitats and natural flowways, improving water quality, and ensuring clean and reliable water supplies for both human and natural environments. As a managing partner of the Everglades Partners Joint Venture, Atkins provided full-service, on-site program/project management support for CERP.
The scope of work included developing plans for monitoring and assessment of all CERP projects, project controls, meeting logistics support, design support, construction administration, technical writing and publication support, and management of a small-business subcontracting plan. Due to the great uncertainty regarding how the planned projects could restore Everglades ecosystem ecological functions, the U.S. Congress proposed including adaptive management—a “learn while doing” approach, as a part of the guiding framework for the projects included in CERP. Adaptive management is substantially different from traditional project management approaches. Atkins took the leadership role in developing a project implementation plan and master implementation sequencing plan, as well as preparing guidance for project managers.
These innovative tools proved essential for critical scheduling and processing needed for project completion. Once complete, the restoration of the Everglades will improve 2.4 million acres of south Florida’s ecosystem, improve water deliveries south to Florida and Biscayne Bays and the southwest Florida coast, and reduce saltwater intrusion that has been accelerated by sea level rise and the removal of water from the surficial aquifer. San Jacinto Marsh is a 350-acre tidal wetland located at the confluence of the Houston Shipping Channel and San Jacinto River. It is also the site of the Battle of San Jacinto, the decisive victory that won Texas independence from Mexico in 1836. The marsh is part of the larger San Jacinto Battleground complex, which is a designated National Historic Landmark that receives an estimated 250,000 visitors annually. One of the few functioning tidal wetlands among this industry-heavy area of Houston, San Jacinto has faced a barrage of modern-day battles associated with coastal erosion and sinking land surfaces.
The marsh scored a big win by being selected as the recipient site for beneficially-used dredge material from a nearby dock expansion project at the Barbours Cut Terminal deepwater port. In turn, the community also reaped the benefit of the dock expansion, which was slated to provide additional jobs and revenue to the region.
We served as the dredging engineer of record and our team successfully designed and completed the project within an accelerated schedule of 20 months, transporting 475,000 cubic yards of dredged material nearly 10 miles from Barbours Cut to San Jacinto Marsh. The dredge fill helped restore 150 acres of intertidal marsh habitat, to mimic the conditions of the battlefield in 1836. By restoring the marsh to its historically-accurate condition, an intertidal habitat was created that promotes growth of native marsh grasses and withstands varying water elevations and salinity levels. To ensure the dredged sediment consolidates successfully with existing material at San Jacinto, we will monitor the restoration site for two years. The Western Dredging Association, which covers the North, Central and South America regions, awarded the project their 2017 Environmental Excellence Award for Navigation Dredging. Reacting to past catastrophic utility failures, the State of Utah needed to identify, inventory, assess, and determine replacement costs for the underground utility systems within the state’s higher education campus and other state facilities.
We were hired to create a GIS database populated with maps, element assessment, and associated information about the utility systems to address this need. We began with pre-planning at each of the 20 campuses involved—collecting data in the form of paper plan sheets, PDF, CAD and GIS files to create a centralized GIS database. Systems included in the project were potable water, irrigation water (to vacuum breakers), sanitary sewer, storm water, electrical, gas, and utility tunnels.
We then populated the database with a full utility assessment including remaining service life—allowing us to estimate the cost of asset replacement. A summary report and maps to assist in capital planning were the final components of the project, but our goal was to support future potential.
The GIS model is a living database—allowing for each institution to upgrade the quality and depth of information contained in the database over time. The final product data is also being submitted to Faithful & Gould (F+G,) our sister Atkins company; they will compile and input the data into the State’s capital-planning software solution—enabling the state and its agencies to see a holistic view of the capital needs of both building and utility infrastructure assets and develop a strategic replacement plan based on criticality.
Ultimately, the State of Utah could use the tool for much more than capital planning. Potential applications include predictive system modeling, design support, maintenance operations, master planning, utility optimizations, and integration into the curriculum.
LSU’s Office of Facility Services worked with us to review and verify all available data sources, consolidating them into a new GIS model—a living database that will allow LSU to upgrade the quality and depth of information over time and as the budget allows. As a first step, we reviewed all available as-built drawings (paper, CAD and PDF), and existing GIS layers to extract necessary information. Key utility data sets developed included: domestic and fire water, chilled water, hot water, storm water, wastewater/sanitary sewer, natural gas, steam, communications, compressed air, electric, and various utility providers with assets passing through campus. As predetermined campus geographic work areas were finished, we provided the new GIS model to aid our survey teams with field investigations, supplementing the data with record drawing reviews to verify subsurface utility engineering (SUE) locations and capture related utility information.
Upon completion of the field investigations, we integrated the survey data with the GIS database to produce a campus-wide utility GIS. Finally, we provided LSU with three days of instructor-led training, focusing on the elements of the model, workflows to maintain the database, and administration of the GIS system. A system that will forecast when renovations/replacements are needed, aids survey teams with field investigations, is used in day-to-day operations and maintenance, and also serves as a decision-making tool on infrastructure improvements for future growth consistent with the campus master plan. In the fall of 2016, the WSSC finished construction on the latest expansion, marking the completion of the $30 million project, and the completion of their goal. For us, it’s a decisive moment in Atkin’s long and fruitful partnership with the WSSC. Since 1996 the WSSC has called on our expertise to make significant changes and improvements to the plant.
The original biological nutrient removal (BNR) project incorporated new and expanded facilities, from preliminary treatment through tertiary filtration. During that project, as part of the client’s team, we evaluated various technologies and construction approaches which reduced the expected $80 million construction cost by $30 million. The 2011 enhanced nutrient removal (ENR) upgrade and expansion project pushed the limits of current standards in wastewater engineering—allowing us to create a cutting-edge design that could be retrofitted into the existing plant while keeping it fully operational. We added a fifth aeration tank, increasing the plant capacity to 26-mgd to allow for planned growth in the region, and converted activated sludge facilities to a flexible MLE or 4-four stage Bardenpho™ process; this will allow the plant to reduce supplemental carbon usage during warmer temperatures, or lower flow to achieve ENR. Additional work included: two new 400 HP turbo blowers, one new 150-foot-diameter secondary clarifier and extension of RAS facilities, seven new deep bed denitrification filters (for a total of 20), a new methanol storage and feed facility, and an expanded solids-handling facility with new centrifuge dewatering unit. The design innovations vital to this project will ensure wastewater is treated responsibly, efficiently and safely—protecting the environment, conforming to State legislation, preserving the Chesapeake Bay watershed, and providing for the growing community of Montgomery County.
The ENR project began construction in September 2011 and was completed in the fall of 2016. In an ongoing problem, Yucca Valley’s 10,000 septic systems have been leaking contaminants—including nitrates, pharmaceuticals, and salts—endangering the town’s scarce groundwater. These systems discharge 180 tons of nitrogen into the ground year-after-year.
That’s enough nitrogen to fertilize 3,760 football fields. The community is under a state order to remove septic tanks by 2025 to protect groundwater. To address this problem, the Hi-Desert Water District utilized our engineering services to design a brand-new wastewater collection and treatment system. This project is the first of three phases to convert the existing septic systems to a public sewer system—protecting groundwater and allowing the Yucca Valley community to grow. The first step will convert approximately 5,000 properties necessitating 77 miles of sewer mains and three sewer pump stations.
At the beginning of the design process, we reviewed all planning assumptions and flow projections, and developed a comprehensive model of the future collection system to meet the needs of Yucca Valley. The proposed collection system is a new system in the community (there were no previous flow projections to use) requiring our design team to rely on our work in other desert communities. The design team focused on reviewing design criteria, evaluating existing water use, and determining when buildout of the community would occur. Our detailed analysis of existing infrastructure and project specifications resulted in significant cost savings to the district and residents. The Phase I system is currently under construction, and we look forward to working with the Hi-Desert Water District as they roll out subsequent phases in the coming years. Responding to a recent population boom, Colorado Department of Transportation has taken a bold step to effect change and transform its aging transportation system by embracing technology. CDOT is investing $20 million to combat congestion and improve safety through the use of intelligent mobility technology in the next year.
As one of three consulting firms selected as advisers on the program, Atkins is serving as an extension of CDOT’s staff—helping to move projects from conception through procurement and construction—facilitating a reimagination of transportation infrastructure through intelligent mobility solutions. RoadX’s goals include: reducing the cost of transporting goods by 25%; turning a rural state highway into a zero death road; and reducing congestion and vehicle emissions on Colorado’s critical corridors. We’re using improved analytics, innovative strategies in autonomous/connected vehicles, and big data to exceed these goals—creating a safer more efficient future. Toward this same end, we’re currently administrating the RoadX: Bicycle & Pedestrian Challenge—soliciting innovative solutions to protect pedestrians and cyclists in Colorado.
Prizes go to both the most creative ideas, and the most effective implementation strategies. Winners will be selected at the end of April.
In launching the RoadX Program, CDOT made a commitment to the aggressive implementation of new transportation technology within the next ten years. Atkins’ partnership brings our considerable experience in intelligent mobility towards facilitating that commitment—making a big difference in the lives of Colorado commuters. For more information on CDOT’s RoadX, the Bicycle & Pedestrian Challenge, and the future of infrastructure see.
One of the most efficient ways to capture existing site conditions is with aerial drones. So when the City of Atlanta recently commissioned Atkins to help demolish and expand the North and South parking garage at Hartsfield-Jackson Atlanta International Airport (ATL), we reached out to software engineering company Autdodesk and drone technology experts 3DR Robotics to orchestrate a drone flight over Atkins’ construction site. Because the site was in the controlled airspace of an international airport, the team needed to obtain authorization from the Federal Aviation Administration (FAA) to conduct the drone flight. As part of the authorization process, 3DR, Autodesk, and Atkins were able to demonstrate that the drone operation (which would be conducted in a critical location between runways) could be performed safely and without disruption to airport users. Part of the requirement for the authorization was that the flight team would be in radio contact with the ATL control tower at all times and performed all operations under the control tower’s authority. On January 10th, 2017, the team legally and safely flew the 3DR Site Scan drone over the parking garage area. The team performed a total of 7 flights, capturing over 700 nadir and oblique images, covering an area of 40 acres.
This is the first FAA-approved commercial drone operation in Class B restricted airspace. The pictures were uploaded to a cloud-based program operated by 3DR, where they were automatically processed into accurate 3D point clouds. The models will be used by Atkins to plan the demolition process and organize construction so to minimize effects on the airport’s daily activities. A major east-west transportation corridor that carries recreational, commercial and commuter traffic through the Rocky Mountains also creates a lot of headaches for those maneuvering through regular back-ups and gridlock. When the Colorado Department of Transportation (CDOT) expressed an interest in using intelligent transportation systems and innovative technologies to decrease gridlock, increase safety and reduce traffic time, we were brought on board to help drive the effort for the I-70 Mountain Express Lane (MEXL). CDOT’s overall vision for improving congestion with immediate, interim improvements led us to evaluate the effectiveness of a tolled peak hour shoulder lane between Empire Junction and Idaho Springs. We expanded existing models to assess traffic improvements, which indicated that travel times could be cut nearly in half in the project area.
Taking an innovative approach to relieve congestion without overbuilding the mountain corridor, a 13-mile stretch of the existing eastbound shoulder was repurposed as a dynamically tolled express lane during peak travel periods. Today, it operates only on weekends and holidays and users pay between four and eight dollars, based on congestion levels (tolls can reach 30 dollars based on congestion levels). With added capacity, the corridor has seen consistent, faster speeds and reduced travel times for all lanes. In its first summer season, throughput increased by 14 percent, travel times in general purpose lanes improved by 38 percent, and the time involved in clearing back-ups substantially improved. Less gridlock. Less time on the road means more time for the good stuff. There’s more to the story.
CDOT received Gov. John Hickenlooper's inaugural Governor's Elevation Award in the Superior Customer Service category. CDOT's successful delivery of this project led to stakeholder support and the lane opening on schedule. The project was also honored with the 2016 Innovative Transportation Solution of the Year award by the Women's Transportation Seminar (WTS). The project was bestowed this honor because it helped solve a longstanding transportation problem in Colorado with an innovative solution. In order to complete major elements of its most recent airport master plan, the City of Atlanta selected the Ascend joint venture (JV) to provide on-call technical, professional architectural, and engineering design services for various projects at H-JAIA.
As the lead firm of the Ascend JV, Atkins has been involved in some of the most notable projects at Hartsfield-Jackson. We served as the project management and design lead for the terminal roadways portion of the $1.2 billion Maynard Holbrook Jackson International Terminal.
The project included structural design of the three-level, landside elevated roadway structures and mechanical stabilized earth walls, as well as an extensive drainage network. The project also included a maze of utility infrastructure that required coordination with multiple utility companies and consultants, as well as several LEED design elements. In addition, we designed new access roadways for surrounding tenants including Delta and the Federal Aviation Authority, along with coordinating traffic signals on Loop Road for shuttle connections to the main terminal. Other services provided by the Ascend JV include development of one of the first electronic airport layout plan (eALP) projects in the country at H-JAIA.
We worked with a team of consultants to develop geographic information system (GIS) data including all airside features, runway and taxiway features, lighting, navaids, obstructions, virtual surfaces, and environmental layers in the airport GIS database. The tool lets airport officials, regional planning agencies and other stakeholders access airport layout plans electronically, saving costs as compared to traditional paper ALPs and helping standardize the process of performing airport and aeronautical surveys. The Doha Metro Red Line South project is part of the overall Doha Metro project being developed by Qatar Rail. The Red Line, also known as the Coast Line, runs for about 40 kilometres from Al Wakra in the south to Lusail in the north and has 17 stations. The line connects Hamad International Airport at Terminal 1 to the centre of the city.
The Red Line South contract comprises c. 14 km of twin-bore tunnels along with five underground stations. Atkins was appointed as Lead Designer in June 2013 by RLS JV, a joint venture led by QDVC, a JV between Qatari Diar and France's Vinci Construction Grands Projects, and including South Korea's GS Engineering and Construction and Qatar's Al-Darwish Engineering. The vision is to provide integrated railway services that are reliable, attractive and be the favoured mode of transport for all. Atkins has been responsible for the multi-disciplinary design of five underground stations, five switchbox structures, four emergency egress shafts as well as functional planning of tunnels/shafts and track alignment design. In addition to the above we are providing expert advice on all fire and life safety issues in establishing the appropriate fire strategy for the stations and tunnels, and assisting the client with obtaining Qatar Civil Defence Department approvals.
The Public Library building is planned as part of the Nabta Town Masterplan in the region of Borg Al Arab, Egypt. Nabta Town, a sustainable mixed-use urban development in the Middle East, is a uniquely smart, urban real estate masterplan that incorporates world-class academic institutions, cultural, leisure and commercial centres, a business park, generous public spaces and holistic housing neighbourhoods. The brief proposes a multiuser learning facility that caters to the needs of both the public and students from nearby academic facilities. The design emphasises an architectural language that is deeply rooted within its context, which encourages the user to ponder, innovate and explore. It forms a landmark public space that encourages dialogue through culturally stimulating spaces that are reminiscent of Egypt’s vibrant heritage.
Atkins worked with Swedish company Hexicon as engineering partner to design the world’s first multi-turbine offshore wind floating platform. Syne System Utilities Cracked. Atkins was pushing the boundaries of design to support Hexicon in maximising energy yield. Experience in innovative, transformational work both in the renewables and oil and gas sectors had enabled the project team to go one step further in making the exciting concept a reality. New developments in the design of the floating structure's mooring system increased the efficiency of the rotating system reducing CAPEX and maximising energy yield. Atkins’ extensive experience in floating wind has played a key role in developing the concept and originally winning the work. The integrated design capability that enables the head to toe design that we were undertaking for Hexicon demonstrates how our experience across a range of both floating and fixed offshore wind projects can add real value to clients.
Atkins has been involved in more than half a dozen floating wind projects around the world including: • Detailed design and analysis for Principle Power’s WindFloat prototype in Portugal • Design for Pilot Offshore Renewable’s Kincardine floating wind project • Winning Statoil’s Hywind floating wind demonstrator Installation Challenge competition. In conjunction with the U.S.
Army Corp of Engineers, Charleston District, Atkins will prepare the environmental impact statement (EIS) in order to evaluate the project’s potential socioeconomic and natural environmental impacts. Conducted over a period of 5 to 6 years, the EIS will address numerous issues such as sea level rise, scenery impacts, protected species and habitat, socioeconomic issues, transportation impacts, noise and vibration, and air quality. The wharf will encompass more than 2 miles, with the ability to manage eight design vessels at full buildout. The expansive size of this project could impact approximately 54 acres of tidal salt marsh and bottomland hardwood wetlands, where threatened and endangered species exist. Among these and several other issues, Atkins will evaluate the project’s impact and develop ways to mitigate the environmental effects.
Developed jointly by the port authorities of Georgia and South Carolina, this bi-state owned and operated marine container terminal will aid projected growth for containerized cargo for a minimum of 25 years and is expected to support economic development in the region, including adding billions in tax revenue and upwards of 1 million jobs. With traffic through this freeway corridor expected to double in the next 20 years, the Nevada Department of Transportation (NDOT) prioritized investment in this critical section of infrastructure to meet the needs of the growing resident and tourist populations. Travelers make 25,000 lane changes per hour in this freeway corridor and as many as 1,400 crashes take place annually.
To boost safety, mobility, and accessibility, roadway improvement plans include separation of freeway traffic from arterial traffic, reduced numbers of merging sections, and connection of high occupancy vehicle (HOV) lanes to create a continuous 22-mile stretch from US 95 through I-15. Considered the most important and ambitious project in NDOT’s history, it also accommodates regional economic redevelopment through improved access to downtown Las Vegas and the Resort Corridor. We serve as lead designer, for design builder, Kiewit Infrastructure West, managing all design and engineering services on this multiphased, multiyear project with responsibilities that include design services for roadway, drainage, bridges and structures, traffic control, signing, pavement marking, landscape, and ITS as well as providing quality control, utility coordination, public involvement, design surveying, and design support during construction. Video courtesy of NDOT. The initial phase of the program was the design and construction of the South Airport Automated People Mover (APM) Complex. As a subconsultant to the prime architect, Atkins is responsible for civil and transportation engineering for the South APM Complex. This initial phase included the design and construction of a new APM station, new 2,400 car parking garage, renovation of the APM station in the North Terminal, completion of the APM guideway structure to the South APM Complex, roadways, bridges, overpasses, site grading, utilities, and all associated infrastructure.
The ultimate STC program will include the South APM Complex as well as an Intermodal Transportation Facility, which will serve as a hub for three passenger rail projects, including a planned $2.2 billion intercity passenger rail line from Miami. Atkins was responsible for planning the entire roadway system for the STC ultimate buildout.
Atkins was also responsible for the design of the loop access roadway surrounding the South APM Complex, including planning and development of alternative roadway concepts for the ultimate transportation master plan addressing the future STC. This effort included roadway plans, stormwater conveyance systems, signing and pavement marking plans, demolition plans, utility coordination, retaining walls, and maintenance of traffic plans. The approximate length of the 2-to-4 lane loop roadway was 3 miles. ITER (International Thermonuclear Experimental Reactor) is the world's largest experimental nuclear fusion reactor in southern France which aims to deliver nuclear fusion on a commercial scale, offering safe, limitless and environmentally responsible energy. ITER is the next step in one of the world's leading energy research programmes, and is bringing together the largest nations in a quest to harness nuclear fusion to meet mankind's future energy needs. Since 2010, Atkins has been architect engineer, in partnership with engineering giants Assystem, Egis and Empresarios Agrupados, as part of the Engage consortium. The consortium is in charge of delivering 39 buildings and associated infrastructure for the ITER project, including the 50 x 200m Tokamak complex.
The 200-strong integrated team of experts from our Energy and Infrastructure businesses are working together to ensure fusion experiments begin on schedule to help meet the challenge of not only decarbonising but also increasing the world's energy supply. Engage is responsible for supporting the procurement process and construction planning and supervision for the buildings including service and site infrastructure. Since 1989, Atkins has performed a wide range of projects at Port Miami. As program management consultant, we provided on-site marine structural engineering and project management expertise in support of the evaluation, design, engineering, and value engineering of over 5,200 linear feet of deep water combi-wall retrofit and strengthening work, designed to accommodate super post-panamax container vessels of up to 216,000 deadweight tonnage. The combi-wall system is comprised of steel pipe piles measuring up to 48 inches in diameter in combination with intermediate AZ sheet piles. The project included design of new 100- and 150-ton capacity mooring bollards as well as high-energy absorption foam-filled floating fenders.
Recently, Atkins completed an in-depth surface and underwater inspection, condition assessment, and structural evaluation of the cruise ship berthing zone seawall located waterside of Cruise Terminal J. The seawall was constructed in 1989 and is made up of 1,487 feet of steel sheet pile combi-wall. Atkins prepared a comprehensive inspection and condition assessment report that addressed the structural integrity aspects of the combi-wall and contained alternatives for long- and short-term repairs, an assessment of feasible restoration methods, and replacement alternative design.
Atkins also provided construction engineering and inspection (CEI) services for 6,000 linear feet of active cargo wharves including 800 linear feet of pile-supported mooring dolphins. Atkins self-performed underwater inspection services for a new sheet pile wall in 45 feet of water and oversaw relocation of more than 150 healthy corals from the existing seawall to an on-port recipient area.
Atkins has completed the flood control master plan updates for the Las Vegas Valley since 1997 (consultant-led updates). Individual flood control plans must be reviewed every five years, and the master plan must be continuously updated to assess progress, identify obstacles, and to recommend changes needed due to growth and development of the area. Over time, the master plan has evolved into a technical tool for guiding local governmental agencies and private consultants in the development of both public and private property. The master plan update process includes data collection, updating land use data, determining hydrologic modeling parameters using GIS capabilities, updating hydrologic models, updating the flood control facilities inventory in a GIS geodatabase, making master plan facility recommendations, and estimating facility construction costs. To support this process, Atkins developed a hydrologic model of over 1,500 square miles, which defines accurate 100-year peak flows and volumes for the entire valley. Atkins also developed a relational geodatabase to represent valley watersheds and associated regional flood control facilities, serving as the foundation for associated modeling efforts. A custom suite of GIS tools was also developed to facilitate the continuous update/maintenance of the master plan.
In addition, an automated cost estimation tool was created to predict the future cost of flood control facilities for more accurate forecasting and planning. The tool summarizes the costs of all facilities in the region, keeping track of the value of flood control infrastructure—helping our client best plan for and provide effective flood controls. © Jeffreyjcoleman Dreamstime.com. This two-berth cruise terminal on the north coast of the Dominican Republic is capable of accommodating up to two post-Panamax cruise vessels, which translates to roughly 10,000 visitors a day. Carnival Corporation estimates eight of its brands will make 140 calls on the port, with 23 ships throughout its first year of operation. In addition to planning, landscape design, architecture, and engineering services for Amber Cove’s structures and amenities, we also designed roadways and the transportation hub that helps visitors take onshore excursions and explore outlying points of interest. The development also includes hillside waterslides overlooking the 5-acre pool/lazy river recreation area, a zipline, a series of shops and restaurants, a destination duty-free shop, and a hilltop food and beverage establishment with a 360-degree ramp access from below.
Echoing the culture and existing architecture in the area, we incorporated modern interpretations of historical periods of significance for the Puerto Plata province. Visitors perusing the 25-acre waterfront development will enjoy an architectural nod to the fortified 16th century, classical-colonial 18th century, and Victorian late 19th century in 25 buildings and multiple landscapes. Atkins also incorporated features that promote self-sufficiency and sustainability including rooftop rainwater harvesting, seawater desalination, a wastewater treatment plant to minimize environmental impacts, and backup generators to ensure uninterrupted utility service.
Wessex Water, is developing its water supply grid to meet demand for the next 25 years with support from Atkins. This will be the largest and most complex project for Wessex Water and is valued at £225m.
The 8 year project includes a 74km transfer main that will run between Sturminster Marshall in East Dorset and Camp Hill in Wiltshire. The grid allows water to be moved from areas with surplus water to other areas which are deficient. This is to improve flows in some rivers and protect their ecology, as well as to improve resilience for example against occasional deteriorating raw water quality. It secures a reliable, constant supply of water which can be maintained 365 days of the year.
Atkins developed the conceptual design and prepared the initial business case for the Optimiser, a sophisticated closed loop control system. We then assessed potential suppliers and helped Wessex to procure and the Optimiser from Servelec Technologies, and to implement it. This included identifying enabling works, and the resources needed to ensure a smooth adoption of the Optimiser solution. The Optimiser, a subset of the grid, has already enabled Wessex Water to respond more effectively to incidents to ensure that supplies to customers are maintained if water treatment plant failures occur, as well as minimising operating costs. The Grid will greatly improve the flexibility of the water network, enabling alternative sources to supply demand (each customer will have two sources). Control of the existing system has traditionally been simple, however, the Optimiser has provided a more flexible control system, which will be address a range of hydraulic and water quality issues to provide cost-effective integrated control of the whole Grid.
The Atkins team set out to equip Southern African Development Community (SADC) member states to manage and respond more effectively to the recurring floods that have destroyed communities. We helped them understand how to reduce the impact on vulnerable populations by mitigating the destruction of property, loss of livelihoods and minimising mortality. We worked closely with the member states to improve their knowledge of flood risk through improved hydrometric data and flood mapping, improve the systems and processes in place and provided case studies to demonstrate how to produce a flood risk management strategy for a given area. This will positively affect 9 million inhabitants living by flood plains and reduce the risk of flooding through the provision of flood risk management tools. The key achievements of the project included an increased awareness of the benefits of sharing data and information, and peer-to-peer learning about successes and challenges through shared experiences. We assessed all of the relevant SADC Hydrological Cycle Observing System (HYCOS) stations and works to ensure that the prioritised stations are functioning and sustainable to provide a better understanding of disaster risk reduction and flood risk management sector issues and approaches throughout the region. We provided guidance in areas of key importance to the SADC Member States, including guidance on flood modelling, flood risk management option appraisal and strategy development, flood forecasting, and the procedure response manual.
We increased the clients and their stakeholders understanding of the level of risk in the region through the flood atlas, and in more detail in two specific hot spot areas. The tools we developed can help to encourage more sustainable Disaster Risk Reduction (DRR) and flood risk management solutions. The pilot hot spot flood risk management strategies and implementation plan provide good practice examples for all SADC Member States in assessing and selecting long term DRR measures. The flood risk maps allows Member States to identify flood risk areas and are a valuable resource for all those interested in effecting change and improving flood risk management.
Atkins has designed the world’s largest drinking water storage facility, in the Kingdom of Saudi Arabia, as verified by the Guinness Book of World Records. The project was delivered by a consortium of Al Muhaidib and Vinci UK with Atkins as sole consultancy service provider. Atkins was the multi-discipline detailed designer for the scheme, completing the civil, structural, architectural, geotechnical, hydraulic, mechanical, electrical and process design of the scheme. During an initial optioneering and innovation phase with the National Water Company, KSA, we developed a range of options including steel, reinforced concrete and precast construction techniques.
As a result of combining technical innovation with collaborative working, our consortium proposed a solution utilising internal post tensioned circular reservoirs to reduce the land take needed and maximise efficient use of the overall site. The reservoirs are strategically important to the Kingdom of Saudi Arabia given the rapid development of Jeddah in recent years and a rise in the demand for water.
The project was part of the first phase of a programme of work commissioned by the National Water Company and are the first reservoirs of this type to be constructed in Saudi Arabia. The reservoirs are currently the largest operational internally post-tensioned circular concrete potable water reservoirs in the world - 120 metres in diameter and 18 metres in height. The eleven circular tanks are hydraulically linked providing a storage volume of over 2 million cubic metres of water – the equivalent of 800 Olympic-sized swimming pools.
The Briman Strategic Reservoir project not only holds the Guinness World Record for the world’s largest drinking facility but more importantly will provide secure water for use during emergencies and during unpredicted situations for the population on Jeddah for years to come. Atkins is a key partner of the eight-strong alliance, eight2o, which has been formed to deliver billions of pounds (£1.738bn) worth of essential work for Thames Water, updating Britain’s biggest water and sewage company. Comprising of five groupings including two design and build joint ventures, which are Costain and Atkins (CA) and Skanska, MWH Treatment and Balfour Beatty (SMB). MWH is the programme manager and IBM is the technology innovator partner, plus Thames Water as both client and partner.
The main projects eight2o are working on are the large water treatment works in London, Hampton, Ashford, Kempton and Walton under the wastewater non-infrastructure quadrant. Atkins have designed the major upgrade of the Beddington Wastewater Treatment Works, with supplier integration using BIM at the heart of the upgrade approach. Atkins has also worked on the Lane End and Southfleet nitrates project and eel screens project to align river systems with EU regulations. The biggest project includes working on the Thames Tideway Tunnel Interface project. Atkins has been involved with the Mogden air main and combined heat and power (CHP) projects, to Ogbourne and Angelinos water pipeline schemes amongst several hundred other projects that are set to be undertaken within Thames Water’s 5 year plan.
These plans have been broken down into quadrants; wastewater and water, and within these groups; infrastructure (underground) and non-infrastructure (above ground). Thames Water is taking this opportunity to achieve greater efficiency in implementing its business plan for AMP6, focusing on team work, sustainability and an integrated supply community in order to deliver strategy and cement long term value to Thames Water and its customers. The overall eight2o work is set to be completed in 2020 with a potential to extend contracts until 2025. Decades of instability were ended when a 300m section of a road near Rothbury was reconstructed by partners of the VBA joint venture (VolkerStevin, Boskalis and Atkins). The B6334 road in Rothbury has been subject to regular landslips over a prolonged period of time, and was frequently closed to traffic. The section was future-proofed by VBA who carried out complex earthworks and site dewatering in order to prevent further destruction. The project addressed the underlying causes of ground instability and dealt with the 2012 landslip that had left damage.
This means the residents of Rothbury will no longer have to take lengthy detours to get to the village. Our team of engineers designed and constructed an anchored bored piled retaining wall in order to support the road.
Their design included an innovative passive dewatering system which will reduce groundwater pressure. Our team made sure environmental enhancements to the SSSI (wood pasture) and provision for wildlife were incorporated. Downhole CCTV footage was used from inside the boreholes to help create 3D models which provided the basis of the design and to gain an understanding of what was happening underground. Most of the complex engineering is invisible to people driving along the new road. Slopes are held in place by retaining walls and 30m long rock anchors bored into the hillside whilst deep wells take the excess water away.
This will have a positive social and economic impact on the town which relies on its income through tourism. As lead consultant, we carried out a major project on the resilience of UK water supplies for Water UK with partners Mott McDonald and Nera Economic, which was completed in the summer of 2016. We produced a report that set out the basis of a long term planning framework that considered the impact of climate change, population growth and environmental factors in order to strengthen the resilience of water suppliers for users across the UK, whilst protecting the environment. Our experience working for individual water companies, UK Water Industry Research (UKWIR), the government and regulators alike, gave us the specific expertise to lead on this project. The report looked at the next 50 years of water provision across the country. We have been working with Kincardine Offshore Windfarm Limited (KOWL) since 2013 as an active member of the development team.
We are developing one of the world’s first arrays of floating wind turbines by 2020 which will establish a leading position for Scotland in the development and deployment of this novel technology. This will be a pilot-scale demonstrator offshore wind farm utilising a semi-spar floating foundation technology, which will demonstrate the technological and commercial feasibility of floating offshore wind. Floating foundations open the possibility for future offshore wind farms to be located further from shore in deeper waters, minimising visual impacts whilst accessing hitherto untapped wind resources. The wind farm will have the capacity to provide 218GWhr of electricity which is the equivalent to powering over 55,000 homes in Scotland, and will see a reduction of over 94,000 tonnes of CO2 compared to fossil fuelled power sources. We have taken the Project from initial concept design to pre-consent determination. The journey has been significant and challenging, and was made possible by our in-house expertise in marine environmental assessment and consenting. The marine and coastal team provided a ‘one stop shop’ for the licensing and assessment of the Project including: • Environmental Scoping Assessment • Environmental Baseline Studies and Reports • Environmental Impact Assessment and Environmental Statement • Habitat Regulations Assessment • Bird Collision Risk Modelling • Marine Licence and Section 36 Applications • Stakeholder Engagement Ongoing project support – containing installation and operation and maintenance include: • Further requirements for marine licences e.g.
Geotechnical/geophysical survey requirements • Further requirements for small works consent applications to The Crown Estate e.g. Scientific equipment deployment • Ongoing support and advice related to defined marine licence and S36 Rochdale envelope to project engineers • Authoring Project Environmental Management Plan • Authoring environmental monitoring programme • Ongoing stakeholder engagement. We helped the Environment Agency to deliver a beach management scheme at Dawlish Warren at the mouth of the Exe Estuary, with an estimated total project cost of over £14 million.
Dawlish Warren is an important wildlife site, designated as a Site of Special Scientifc Interest, Special Protection Area, Special Area of Conservation, a Ramsar wetland of international importance and local nature reserve. A key challenge was to enhance the role the sand spit plays as a flood defence to the Exe Estuary but not impact on the conservation features for which it was designated. We were involved in all stages of the scheme including: strategy, project appraisal, outline design, Preliminary Environmental Information Report, detailed design and Environmental Impact Assessment. Dawlish Warren Beach Management Scheme Our key marine and coastal environment services included: • Specifcation and management and analysis of required marine surveys, including ecology, UXO and bathymetry • Wave, plume and tidal modelling and reporting • Water Framework Directive assessment • Habitat Regulations Assessment • Environmental Impact Assessment • Coastal impact study • Stakeholder engagement (including 3D printed model of the scheme). The scheme will involve the removal of gabions from the beach to re-mobilise the dunes, beach nourishment using sediment from subtidal sandbanks, repair of groynes to help control the nourishment and development of monitoring and management plans. Used with permission of copyright owner, Environment Agency.
A joint venture between Atkins and Arup has been appointed for a consultancy contract to deliver a range of design and engineering services for BMB; the joint venture between BAM Nuttall, Morgan Sindall and Balfour Beatty, who have been appointed by Tideway to deliver the West section of London’s new ‘super sewer’, the Thames Tideway Tunnel. Valued at £416 million the six kilometre ‘West’ section of the 25km Thames Tideway Tunnel will run from Acton in West London to Wandsworth in South West London incorporating seven separate work sites along the route. Works will include design, construction, commissioning and maintenance following construction completion. The new tunnel will be the biggest infrastructure project ever undertaken by the UK water industry. The completion is scheduled for 2022.
Atkins was appointed by Surrey County Council to help reduce flood risk in the county. As part of our services, we developed and implemented an innovative solution to prioritise areas at risk of flooding for further investigation across the whole of Surrey. As a Lead Local Flood Authority (LLFA), Surrey County Council is responsible for managing local flood risk from groundwater, surface water and ordinary watercourses. The Surrey Flood Risk Partnership Board, a local stakeholder group, meet on a regular basis to discuss the priorities for investing in flood risk. The prioritisation tool provides the group with most relevant, readily available data to quickly identify which areas in Surrey had the greatest need for managing flood risk on a strategic level. The flood risk prioritisation tool is a GIS based multi-criteria tool that incorporates the flood risk information from multiple theoretical and historic data sources including Environment Agency flood map and records of property flooding collated by Surrey County Council.
The tool provides a strategic overview of flood risk across the whole of Surrey in a simple and easy to use format. This project was completed in 2013 and is updated annually.
The latest version incorporates flood economic data using Atkins flood economic tool, Flood DamaGIS. This enhancement allows Surrey County Council to consider the potential for a viable economic business case as part of the prioritisation. Atkins also developed an excel based tool, which works alongside the GIS, enabling the client to adjust the weightings applied. This allows the client to quickly assess the impact of changing priorities, such as focussing on reducing surface water flooding or considering the priorities of local stakeholders, without needing expert skills in GIS.
Atkins, working with Arup, has been appointed to work with Severn Trent Water Ltd. As part of their clean water strategic grid team. A key part of the grid is the Elan Valley Aqueduct, which is 120 kilometers long and provides water to Severn Trent's customers in Birmingham. Completed in 1906 and now in continual operation for over 100 years, increasing water demands of the city mean the infrastructure is beginning to show its age.
Using expertise from our multidisciplinary teams, we established options for the proactive maintenance and replacement of several sections of the Elan Valley Aqueduct (EVA). The objective of the work is to achieve Severn Trent Water’s aspiration for an asset fit for the 22nd Century. Using our extensive water and tunnelling experience, we developed the outline design for the selected schemes, provided planning support and environmental guidance and assisted the client in compiling tender documentation for a design and build contract. The package of 3 schemes covers 4.2 kilometres of 3 metre diameter tunnel, with a capital cost of around £70million.
This was undertaken as part of a 10 year Engineering Consultancy Framework under which we assist Severn Trent Water in prioritising assets for investment and promoting the best TOTEX solution in achieving the best outcomes for STW and their customers. Liverpool Wastewater Treatment Works (WwTW) had problems with the existing, second stage treatment Baff plant blocking up, which led to premature discharges from the works to the River Mersey.
A more robust treatment process was required and it was decided that a sequencing batch reactor (SBR) would be built on two levels within Wellington Dock adjacent to the existing works. GCA JV, a joint venture between Galliford Try, Costain and Atkins, was chosen by United Utilities (UU) to carry out the upgrade of Liverpool WwTW. UU recognised that to successfully deliver this complex project, a different approach to 'design and build' was required and a ‘One Team One Aim’ initiative was developed. The team was a special partnership of client, contractor and supply chain, working together to ensure the successful design and build of the new works. All the team were located at the Liverpool site to ensure close collaboration, ownership of the problems and establish a commitment that the team would ‘fix’ Liverpool together. A successful tool for the team was using BIM, which was relatively new in the water industry at the start of the project (2013), but was recognised by the team to be invaluable in ensuring the success of this and future projects in AMP6.
They therefore pioneered its use, ensuring the Liverpool project was at the forefront of BIM technology, setting the standards for AMP6. Following the successful performance of the Liverpool team, UU intend to adopt the collaborative one team ethos to spread the ‘Liverpool magic’ across their upcoming AMP6 major projects. By replacing a 5,300-foot general aviation runway with a new 8,000-foot commercial service runway, the airport has been able to increase its capacity and flexibility in handling larger commercial jets. The expansion of Runway 10R-28L was critical to the airport’s long-range development capacity goals and the overall U.S. Air traffic system, increasing aircraft operations from 80 operations per hour to more than 100.
Atkins served as lead designer responsible for the replacement and expansion of Runway 10R-28L and associated taxiways, leading a team of 16 specialized and local subconsultants. As project manager/engineer-of-record for the $791 million expansion, Atkins developed the design criteria package for the elevated bridge-tunnel structure, using a design-build methodology. It’s only the second time a runway in the U.S. Has been elevated for active roads and rail. The expanded south runway and parallel taxiway extend over the existing airport perimeter road, Florida East Coast Railway, and US Highway 1. Atkins also performed construction administration and oversight for the project, which is among the largest construction projects of its kind to be undertaken in the U.S.
Throughout the course of the project, an estimated 11,000 temporary construction jobs were created, with a $1.4 billion impact to the regional economy. The project was awarded Commercial Airport Project of the Year by the Southeast Chapter of the American Association of Airport Executives (AAAE). The largest component of FasTracks, the Eagle public private partnership (P3) project, unites three corridors and will more than double the Regional Transportation District’s (RTD) current transit system when the final line opens in the fall of 2016.
The project’s three corridors stretch over 36 miles from Wheat Ridge and Arvada in Denver’s west suburbs to the Denver International Airport on the city’s eastern side. In June 2010, RTD selected the Denver Transit Partners (DTP) team to design, build, finance, operate and maintain the Eagle P3 project. This includes the University of Colorado A Line to Denver International Airport, B Line to Westminster, the Gold Line (G Line) to Wheat Ridge and Arvada, and a commuter rail maintenance facility. Our role on the DTP design team included corridor management and design for the trackway, roadway, and structural elements for portions of the University of Colorado A Line and design for trackway, roadway, drainage, and structural elements of the B Line to Westminster. These corridors involved grade crossings, overhead structures, and underpasses in several jurisdictions. With a significant number of stakeholders and multiple projects in progress, effective coordination and communication was critical to manage interfaces with outside projects, internal project components, and operational requirements.
The University of Colorado A Line is particularly important to Denver residents and visitors as it extended rail service to Denver International Airport—located 25 miles outside of downtown Denver—providing cost-effective and reliable transit to the airport. Prior to the start of the Eagle P3 project, Atkins worked closely with RTD to conduct an alternatives analysis and prepare the Environmental Impact Statement and preliminary engineering for the East Corridor (now called the University of Colorado A Line).
The study, which included extensive public outreach, documented the transportation and environmental impacts associated with transit improvements in the area. A wide range of possible alignments, technologies, and station locations were examined to support the development the FasTracks program.
The University of Colorado A Line opened on April 22, 2016 and the B Line to Westminster opened July 25, 2016. Atkins produced the detailed design for E.ON’s Humber Gateway offshore wind farm’s offshore substation support structure.
Harland and Wolff Heavy Industries Limited delivered E.ON with a full design and build package with Atkins subcontracted for the module support structure design. This project was awarded to Atkins because of our geotechnical expertise and capability to develop feasible foundation designs for the chalk ground conditions. The offshore substation platform substructure consists of two components; a piled jacket and a module support frame (MSF) that was lifted onto the jacket substructure on site.
All work was performed with due consideration to the difficult ground conditions and a key project requirement to enable installation using the project’s jack-up vessel – the MPI Adventure – which imposed restrictive load curve limits on geometry and weight. This enabled the developer to make optimal use of long term charter arrangements and mitigate installation risks. The MSF provides support and allows access to two topside modules. The modules are connected to the foundation through eight support points, four per module. The modules connect to the wind farm by eight array cables each and are connected to land by one export cable each. Atkins conducted: •Full in-place, load-out, transportation analyses •Lift structural analyses for both structures •Fatigue, ship impact and on bottom stability analysis for the jacket substructure •Detailed design drawings based on calculations for fabrication at Harland and Wolff’s shipyards in Belfast. The work took place during 2013, and was completed in 2014.
Humber Gateway is located in the northern part of the Greater Wash area. The site is around 8km east of the Yorkshire coast near the Humber Estuary in the North-East of England. Skyrim Dragonbone Crossbow Mod Download. The wind farm has an installed capacity of 219MW, consisting of 73 3MW Vestas V112 turbines and a single twin circuit 33KV to 132KV substation. The wind farm provides 170,000 homes with green power. The National Signalling Framework has been established to modernise and improve signalling infrastructure across the UK network.
Atkins was awarded contracts for the Anglia and Kent area and the Sussex and Wessex frameworks in January 2012 for seven years. Services provided by Atkins include specialist signalling systems design, installation, testing and commissioning, and the associated power, telecommunications, ancillary civil engineering and OLE designs. The framework was set up to deliver design and build contracts (GRIP 5-8) but at the time that Atkins was appointed, the initial development stage (GRIP 1-4) also needed to be done. Given Atkins’ signalling expertise, we were given an additional commission by Network Rail to progress several key projects to the design and build phase so that they could then be delivered under the framework. On East Kent Resignalling Phase 2 (EKR2) will see a 33-mile stretch of the region’s network upgraded and a brand new station has opened at Rochester, delivering a more reliable and efficient rail service with five extra trains to London during the morning peak and longer platforms. The scheme is upgrading an area last renewed in 1959 and is part of Network Rail’s strategy to transfer control of signalling systems to Regional Operating Centres.
Our team has developed a range of innovations designed to save time on the scheme including the introduction of a new software package to assess assets along the project route. Working with Gioconda Limited, virtual reality software was created which allows the signal designer at the outline design stage to do everything they could if they were on-site but in a fraction of the time. Signal sighting can usually take up to nine months for a project of this size, but the software solution saw the work completed in just four weeks by one person at their computer without the need to go on-site. Not only has this pioneering solution cut six months from the outline design phase but has also made savings in terms of site protection staff while significantly reducing occupational health issues associated with travelling to and from site and working in an operational railway environment.
The HD video that was produced has been distributed to the design, construction and testing teams so that their site visits have been dramatically reduced too. The collaborative nature of the framework contracts means that knowledge and best practice gained on one scheme will be applied to the others to provide value for our client. Atkins was lead consultant on a demanding project to upgrade Belfast’s ageing Victorian sewer system. One of the largest infrastructure projects to be undertaken in Northern Ireland, the scheme had to contend with high volume stormwater flow and challenging geology.
The scale of the project was immense, including the construction of 9.5km of tunnels, 21 access shafts and a pumping station housed in Belfast's deepest and largest excavation. We provided project management, planning, preliminary design, contract supervision and administration to improve water quality in the River Lagan. The new infrastructure means that the Belfast sewers are now able to deal with a one in 30 year storm event, an event magnitude that has since become an industry standard. Dubai Opera will be unique for a venue of its size, in that it will have the ability to convert into three modes; from a theatre into a concert hall and into a ‘flat floor’ form, offering 2000 m² of space for events such as exhibitions and gala events.
What makes Dubai Opera so important is the new offering it will bring to residents and visitors of the city. It will become a hub for cultural activity, entertainment and artistic expression, while playing its part in creating a vibrant local community.
Dubai Opera aims to transform the emirate’s cultural footprint and establish the city as a part of the elite global theatre circuit – providing a vital new draw for the tourist industry – a cornerstone of Dubai’s economy. Dubai Opera opened on 31st of August 2016 with a sold out performance by Placido Domingo. Go here to read more about the and the.
It implies the symbiosis of three main components – Office, Hotel and SOHO apartments. Although these buildings can be operated individually but while they function together, a powerful urban synergy is created from these separate entities. Total GFA is 246,067 sq.m with a plot ratio of 12.6. It comprises of three 165.8m tall building, a 39 storey office tower, a 38 storey Hilton hotel and a 43 storey SOHO apartment. The crystalline building form signifies its status as the landmark in the city of Chengdu, with its modern and geometrical expression in curtain wall, has given the project a pure and classic appearance.
East West Rail (EWR) is a major programme to establish a strategic railway connecting East Anglia with Central, Southern and Western England. The programme is divided into a number of sections and phases which are being led by Network Rail. Atkins is involved in a number of these, charting the journey of the scheme from its inception to its entry into passenger service. The programme will boost regional connectivity between Oxford and Felixstowe, driving social cohesion and galvanising local economies by connecting people and businesses to jobs and services.
Phase 1 Atkins provided the technical design for the Chiltern Railways Bicester to Oxford main line railway. This involved the design of a brand new, 20-kilometre long, twin-track section of 100mph railway between Bicester and Oxford, the building of a new station at Oxford Parkway and the upgrading of stations at Bicester Town and Islip. The design expertise provided by Atkins includes project and engineering management, track, civils, mechanical and electrical systems, telecommunications, signalling, electrification, surveying, highways, geotechnical, drainage, utilities, architecture and environment, plus engineering safety management. This award-winning project is complete and Chiltern Railways trains have been operating services from Oxford through to London Marylebone since December 2016. It is the first new line connecting a major city to London for over 100 years.
The scheme had a phased opening and was officially opened to passengers in a ceremony led by the Secretary of State for Transport, Chris Grayling, on 12 December 2016. EWR1 was delivered by the Bicester to Oxford collaboration, which consists of Chiltern Railways, Network Rail, Carillion Buckingham Joint Venture, Atkins, Siemens and RSK.
Phase 2 The Phase 2 project covers the remainder of the Western Section of EWR. Atkins has partnered with Network Rail, Laing O'Rourke and Volker Rail to form the EWR Alliance, which is contracted to deliver a full range of services from early feasibility studies through to the design, engineering, testing, construction and commissioning of the scheme. This includes the preparation and submission of a Transport and Works Act Order.
The works consist of a major route upgrade and the re-opening of unused lines, featuring 100 kilometres of new track, new stations, a new signalling system and over 20 new bridges. The redevelopment of the port will transform Muscat’s current commercial port into Oman’s premier waterfront destination ensuring integration with and enhancement of adjacent historically sensitive areas including Muttrah and Harat Al Shamal. With a GFA of approximately 350,000 m 2 new mixed use area, the new port hopes to support the government’s drive towards a diversified economy by creating up to 5,000 direct jobs and accommodating up to 10,000 visitors per day. The redevelopment will enable increased international cruise liner arrivals and has the potential to operate as a dedicated home port. Atkins was appointed by Five Holdings as lead designer for the 60-storey tower, which is to be located in the heart of Jumeirah Village, off Sheikh Zayed Road in Dubai. The tower comprises a mix of serviced apartments and a five-star hotel – the first five star property in a five-kilometre radius. The sky lobby located at the top of the podium accommodates a spa, all-day-dining restaurant, health club, meeting rooms and a landscaped podium roof.
The hotel part of the tower comprises 247 hotel rooms and suites, whereas the residential accommodation includes 221 one and two bedroom apartments and 33 four-bedroom apartments with private pools. The concept is based on a 30 degree rotation of each floor thus creating a series of lush-green balcony sky gardens and 271 sky-high swimming pools. To most people, the M25 is 440km of motorway, a daily commute or a punchline. But to a small group of specialists it is most visible as a stream of data.
From thousands of cameras and other sensors, they see progress, air quality, climate, accidents and repairs. In June 2015, Atkins teams in London, India and the US joined forces with innovation partners Fluxx and Connect Plus Services, the organisation that manages the M25, to develop innovative ways to use this data to improve the lives of commuters. The brief was simple; deliver intelligent interventions to improve travel experiences “I know the pain that people suffer on the M25, and seeing the data that we collect being used in a completely different way, the benefits it unlocks, is brilliant,” said Tim Hughes, Intelligent Mobility product manager at Atkins.
This event, organised by the Atkins Digital Incubator, represented a new way of working. “How do we drive value more quickly?” asks Atkins' CDO Richard Cross, “Not spend months thinking, but develop something quickly, experiment and improve?” “What’s crucial is having the transport planners in the room,” said product manager Ashkan Miri. “They’re working directly with developers to build the vision of the product they’re working on.” To learn more about digital engineering or book a visit to the, contact Gary Wilson. Atkins On The Go was the first app that Atkins had ever built, and it was a very successful trial of several new ways of working. With innovation partners Fluxx, we wanted to build a tool that was as useful as possible for our 18,000 staff around the world. We did this by involving staff at every stage in the process. We started with an open invitation from CIO Richard Cross, who wrote to every member of staff inviting suggestions for what the app might do.
This crowdsourcing project was spectacularly successful, with over 400 responses in just the first two hours. It became apparent that timesheets and expenses were the key things, but staff also suggested bigger, even more innovative ideas; using phones to grant access to buildings, or building an Atkins car sharing system around the app.
It was also crucial to involve everyone in Atkins, not just the vocal minority who responded to Richard’s email. So the team ran a detailed persona study, to understand the needs of specific groups within Atkins. Their research focused on people working on site.
They were the group we were most keen to reach with the new app, but also the group least likely to rapidly respond to an email appeal. Interestingly, we had about 50 requests suggesting that email and an address book would be useful on mobile. These were both things that were already possible in the existing system, but a significant minority hadn’t realized. That made it clear that education and training was as important as developing new features.
Staff were involved all through the process of developing the app. A pop-up user testing lab was built, where prototypes and mockups were shown to users, and thier feedback incorporated.
The Timesheet app is now live across Atkins, with new functionality on the way. To learn more about digital engineering or book a visit to the, contact Gary Wilson.
“We’ve had this problem since the airport opened,” said Richard Harding, Head of IT Strategy and Innovation at Heathrow. “What information can you provide to passengers when they arrive?” In February 2016 Atkins, Heathrow and innovation partners Fluxx joined forces to help answer this question at a two day Rapid Start event. The brief was simple: “How can we improve the arrival experience from an hour before landing to onward transport?” Multinational teams in Dubai, India, Hong Kong, Heathrow — and one in a carriage on the Heathrow Express — worked together for 32 hours, developing ideas, building prototypes, talking to passengers and deploying experiments in the arrivals terminals. The teams were multi-skilled, bringing together diverse skills from Atkins and Heathrow including coders, designers, customer-facing service staff, back office technologists, baggage handling experts and members of the Heathrow Express team. The event started with insight and inspiration from innovation partners Fluxx, sharing customer experiences from Hong Kong, Singapore and Heathrow, interviews with passengers and operations staff.
More than 25 ideas were pitched and voted on, with winning ideas including a personalised navigation app, an iPad-based bag tracking system, a personal virtual assistant for arriving passengers and intelligent signage systems. Teams were formed around winning ideas, which were prototyped and deployed over the next two days. “The energy in the room was just fantastic,” said Justin Stenner, Head of Technology for Heathrow Express. “You guys have looked at these problems through a passenger lens,” said Chris Annetts, Heathrow’s Director of Commercial Passenger Services, “Bringing so many creative ways to solve these problems. Many of these ideas we’ve thought about for a very long time as an airport, but haven’t quite cracked them. This lets us get started with a very small budget, to test things and make progress.” “I’ve been absolutely blown away,” said Heathrow Airport CIO Stuart Birrell. “The different thinking, the ideas and innovation, has been fantastic.
I’ve been around airports for many years. “You think you know your business, you think you know the industry, but you get a team like this together and it really challenges some of your assumptions. The opportunities we have are just fantastic.” To learn more about digital engineering or book a visit to the, contact Gary Wilson. At Atkins, we’re able to combine decades of deep engineering experience with the tools and techniques of innovation.
The work of the Digital Incubator—and our innovation partners Fluxx—helps us to understanding the hype cycle, enabling us to help clients make the most of new technology. We’re then able to use our global network to empower Clients to work faster and smarter than ever before. For example, we worked to help clients use unmanned aerial vehicles, 3D scanning, data analysis and virtual reality to dramatically improve asset management in large and complex sites. This video shows geomatics consultants Charlton Bland and Kevin Ballard scanning and analysing complex visual and radar scan data. Multiple data sets can be combined to provide intelligence for decision support; predicting collapses before they happen. The film shows how this rich 3D mapping can be used in a virtual reality environment for purposes as diverse as staff training or public consultation. To learn more about digital engineering or book a visit to the, contact Gary Wilson.
The Atkins-designed Figbury Lodge Care Home is a new 80-bed facility for residents of the Borough of Poole. The care home specialises in dementia care and includes a unit especially adapted for resident rehabilitation following hospital treatment. The new facility creates a ‘home’ for residents and goes towards addressing a national shortage of quality and affordable care home beds. Our designers created a welcoming sense of familiarity for residents by recreating the enduring childhood image of a home being a two-storey house with a pitched roof, smoking chimney, windows and a door. The form of the care home is split into two wings, each accommodating 20 bedroom clusters on both ground and first floors, with a central body accommodating the entrance, staff facilities and multi-use spaces. A central garden connects to another, more informal garden to the south.
The simple form and layout of bedrooms is interspersed with communal facilities to mitigate long corridors, enabling residents to easily access the garden areas from several locations, with unrestricted wandering within a secure environment. To meet BREEAM targets the project includes sustainability measures such as photovoltaic systems on the roof to generate renewable electricity. Energy and water efficiency will be monitored through the building management system with the intention of reducing the overall running costs for a care home. This building will stand out with its simplicity, bold and clarity in design that signify the corporate culture and image of the bank as well as the characteristic of the financial industry. While people are familiar with the iconic Bank of China tower in Hong Kong, soon a new signature tower will appear in the skyline of Jiangbeizhui, the Central Financial District (CFD) of West China. Bank of China Tower is the new beacon of fortune and prosperity in Chongqing. This 198-metre high iconic tower is designed by a world class architects – Atkins.
Atkins is a famous international architecture and engineering consultancy – largest in the Europe and Top 4 in the world. Atkins has more than 200 offices in 80 countries and regions. This building is perfectly situated in a premium location.
The designer of BOC tower incorporates an advanced design approach in terms of sustainability, energy saving, intelligence into the local context, and creates a high rise tower which is transparent, modern, and dignified. A quarry is a rather unlikely destination for a swank hotel. Perhaps that’s what makes the concept of Songjiang Quarry Hotel so awe-inspiring. Indeed, design and engineering consultancy Atkins won an international design competition for the five-star hotel back in August 2006 and their vision is in the process of being transformed into reality by Chinese developer Shimao. The satellite town of Songjiang is approximately 35 km from Shanghai city centre and well connected to existing transport infrastructure. Sprawling landscapes and natural beauty have made it a popular tourist destination and the district has been designated as an important local and national leisure resource. The design of the Songjiang Quarry Hotel is meant to reflect the natural landscape of the quarry.
The winning concept was inspired by the stunning location and the natural environment of the rocky cliffs, waterfalls and surrounding hills. The project will see the construction of a five-star, 383-bedroom hotel built into the side of a disused, 90 m deep, water filled quarry. The hotel will be operated by Intercontinental as a sport and leisure-oriented spa resort. The concept design has attracted tremendous interest across the world. Apart from the green roof, it is intended that many features, ranging from geothermal energy to solar energy utilization, are included in this project. The reasons for the green roof are two-fold: it is both for the building to fit seamlessly into the surrounding environment and become a ‘natural’ part of the local topography, and also for its eco-friendly and energy saving qualities.
Apart from an awe-inspiring location, a cascading waterfall from the top of the quarry into the pool below it, and striking waveform architecture, the Songjiang Quarry Hotel will have plenty to offer. The futuristic hotel features underwater public areas, guest rooms and conference facilities for up to 1,000 people, and also includes sport and leisure centres. Two underwater levels will house a restaurant and guestrooms facing a 10 m deep aquarium. The lowest level of the hotel will contain a leisure complex with a swimming pool and water-based sports.
An extreme sports centre for activities such as rock climbing and bungee jumping will be cantilevered over the quarry and accessed by special lifts from the water level of the hotel. Also, a transparent glass ‘waterfall’ located in the centre of the building is a major architectural feature. By building the hotel where it is, designers and developers hope to prevent further damage to the ecological environment around it. The Songjiang Quarry Hotel may become just about the greenest hotel ever made. With a height of over 460m, this will be the tallest building in Vietnam. The 81-storey development is located in Vinhomes Central Park - one of the most prime locations in Ho Chi Minh City, Vietnam. Its frontage faces the beautiful Saigon River, and is conveniently connected via major road and water transportation.
Featuring a modern and unusual architecture design that symbolises the diversity and fast-emergence of Ho Chi Minh City, this mixed-use development involves space for hotel, serviced residential apartment and retail. At the base of this skyscraper is a sumptuous shopping centre featuring the finest retailers under one roof for a top-class shopping experience.
The 241,000m2 development will also feature contemporary landscape design that merges natural beauty into this building. Challenge Heathrow Terminals 1 and 5 host both international and domestic flights. The Airport wished to find a solution that would meet the UK Border Force requirement to ensure that passengers cannot swap their boarding cards once they have cleared security and then leave on a domestic departure when they were cleared originally for an international flight.
Importantly, any implementation also had to balance the conflicting factors of security, cost and speed of use. Solution Atkins worked with Aurora to implement its Passenger Authentication Scanning System which uses biometric facial recognition to link a passenger to their boarding pass. The system amalgamates online check-in, airline data, biometric facial recognition technology and departure lounge systems into one seamless ‘end-to-end’ solution. In order to accommodate the varying lighting conditions that are found in the Terminal, PASS employs infrared technology to secure facial recognition of a passenger. Thanks to comprehensive trialling, bench testing and close working with the client, PASS carefully balances the three competing factors identified by the Airport. The system offers quick and simple identification capture and enrollment, it operates on Heathrow’s standard client and server machines and it meets the stringent standards of the UK Border Force.
Outcome PASS has been in operation at Heathrow since 2012 and since its inception has successfully processed millions of passengers. This solution is now being extended in Heathrow’s Terminal 5 with the introduction of Self-Boarding channels which will allow passengers to board their flight using a self-service gate. In recent years, the Louis Armstrong New Orleans International Airport (MSY) has seen a dramatic recovery from its significant underutilization in the wake of Hurricane Katrina.
With enplanements rebounding to pre-Katrina levels, focus has turned from recovery and short-term development to its long-term infrastructure needs. Critical sections of the terminal and support facilities—currently more than 60 years old—have exceeded their useful life spans and must be replaced. In 2012, the City of New Orleans and the New Orleans Aviation Board selected Crescent City Aviation Team (a joint venture) to oversee the airport’s return to a world-class airport in both form and function. The team is working to create solutions that demonstrate a balance between respect for the area’s unique heritage and the need to innovate in a sustainable way that re-declares the relevance of the airport, City, and region.
Atkins has provided a full range of planning, engineering and architectural services for the airport’s long-term development. Called “the most transformative project for New Orleans since the Superdome” by Mayor Mitch Landrieu, the multi-phase project requires an alternative site location concept and layout, a new terminal facility with expandability to 42 gates, a new airfield apron to support the terminal, roadway improvements for access and circulation, and on-site parking facilities. Travelers to New Orleans will be welcomed with the natural hues and tones of the native landscape and the elegant architecture of the City. Layers of stone tile, metallic wall coverings and porcelain will tile throughout the new North Terminal, reflecting the design inspiration of brass trumpets, oyster shells, and misty cypress groves.
The development will serve as a gateway that melds the region’s unique colonial past with its cosmopolitan present, supporting the emergence of New Orleans as a destination city. Our work on the Doha Metro is helping Qatar improve transportation and infrastructure across the city. The programme is critical for the 2022 World Cup and is central in delivering Qatar’s 2030 vision.
We were appointed as lead designer by the ALYSJ JV to deliver the Gold Line Metro stations comprising 13 underground stations and 16km of twin bore tunnels. Our role on the Gold Line includes architectural design, station planning, structural, design of twin bore tunnel, geotechnical analysis and site investigations, site monitoring of AGI Works, design of excavation support, fire and life safety strategy, alignment design, support of the client’s requirements, management and systems assurance and additional works for mechanical and electrical building services design. Once complete, the Doha Metro will reduce congestion and pollution while offering sustainable, attractive and fast public transportation choices for the first time.
We are helping Riyadh by dramatically improving transportation across the city through the design of the metro. We were appointed as lead designer (in a joint venture with Typsa) by FAST consortium to deliver three of the six lines that will comprise Riyadh Metro.
This design and build package includes 25 stations and two depots, 63km of track, with a total capital cost of approximately £7.8bn. Atkins is drawing on its multidisciplinary team of around 250 specialist staff from its offices in Riyadh, the UAE, Bangalore, Hong Kong and the UK. Once complete, the Riyadh Metro, currently the largest public transportation project in the world, will reduce congestion and pollution while offering people sustainable, attractive and fast public transport choices for the first time.
Bourges Boulevard is part of a major ring road around Peterborough, forming a key gateway into the city. Atkins was commissioned by Peterborough City Council to redesign the pedestrian areas of Bourges Boulevard and create better connections between Peterborough train station and the city centre as part of a £4m improvement scheme. The design proposals looked to encourage development within this area, enhance the visual appearance of a major city gateway and improve the provision of pedestrian and cycle facilities along and across the Boulevard. The main outcome was to enhance the aesthetic quality of the street. This has been achieved by the introduction of large-scale street trees, a distinctive new paving arrangement and a suite of new street furniture including lighting and cor-ten planters. Other measures included narrowing of the carriageway and the introduction of two 10m-wide toucan crossings to provide easy ground-level connections to the city centre.
The works in the central area comprise the excavation of below ground ticket halls, running tunnels, station platform tunnels and access passages with links to existing London Underground Stations. One of the biggest challenges of the project is undertaking tunnelling works under Central London where protection of the vast network of existing 3rd party utilities, tunnels, structures, railways and historical buildings is key to the success of the project. Atkins' engineers seconded into the Crossrail project have been responsible for the damage assessment and the design of mitigation to protect 3rd party assets from settlement induced damage. The assessments were undertaken in accordance with a robust phased approach to ensure consistency with focus placed on the most sensitive structures. Timely resolution of concerns with stakeholders and 3rd parties was key to securing “letters of no objection” to allow construction to progress. The extensive 3rd party asset information assembled during the design phase was carefully managed and organised, allowing it to be integrated as a key data set into the Crossrail’s BIM system. Over 3400 buildings, 640 structures (including London Underground tunnels and other rail assets) and up to 14,000 utilities (gas, sewer and water mains) have been assessed to date.
The design engineers have since moved onto the various sites acting as asset protection engineers, bringing with them technical skills and in depth knowledge to ensure continuity to the project across all the Central London bored station and tunnel contracts. As part of the project management team, our engineers continue to advise the client on all issues relating to 3rd party asset protection, accounting for the actual works being undertaken and the ground response on site. Upon completion, phased from 2018, the line is expected to carry 78,000 passengers per hour through 38 stations travelling from Maidenhead and Heathrow in the west, to Shenfield and Abbey Wood in the east. Liantang/Heung Yuen Wai Boundary Control Point and Site Formation and Infrastructure Works – Contract 2 The project is one of the major construction contracts of a new cross-boundary connection in Hong Kong between the boundary control point near Heung Yuen Wai and Fanling Highway to provide a strategic and direct new transport link to serve the cross-boundary goods vehicles and passengers travelling between the northeast New Territories and Shenzhen East on Mainland China. Atkins is employed by Dragages (Hongkong) Limited to be the design consultant firm for the detailed design of a 4.8-km-long dual two-lane Lung Shan Tunnel excavated by tunnel boring machine (TBM) and Drill-&-Blast techniques, mid-ventilation adit, and temporary site formation at portals with other associated works.
One of the key challenges for Atkins is to carry out the detailed design of 12.5m ID TBM permanent lining for double tube tunnels in various ground conditions and form a numbers of underground cross passage openings with 6m span in soft ground underneath public area with shallow ground cover. The new complex was constructed on a 50-acre site on U.S. Highway 90, about 6 miles north of the U.S./Mexico border. We designed several facilities including the 50,000-square-foot border patrol station and provided design for site grading, drainage, and paving. The project incorporated an integrated delivery process that leverages our experience using AutoDesk’s Revit building information modeling (BIM) software to provide closely coordinated, quality construction documents.
This resulted in minimal issues during construction period, ensuring the facility could be built in a highly remote and austere location. Located in an extremely dry and arid environment, conservation was a top priority. With this in mind, we designed the complex to comply with LEED Silver certification requirements and native plants were used in landscaping to reduce water consumption. USBP agents undertake some of the most dangerous responsibilities in U.S.
Law enforcement, including detection and apprehension of subjects responsible for illegal incursions into the United States. To ensure the safety of agents working at the station, the facility was designed according to USBP physical security requirements and to meet Forced Entry and Ballistic Resistance of Structural System standards established by the Diplomatic Security Bureau of the U.S. Department of State. The Connector is instrumental in relieving traffic congestion in historic Ybor City and improving freight access to the Port of Tampa. It also provides an additional hurricane evacuation route and enhances emergency access for first responders. Atkins served as lead engineer on the $426 million project, and as the primary designer of the Connector’s southern portion (80 percent of the overall construction effort). Innovative features include a toll gantry that saves FDOT an estimated $10 million in capital and maintenance costs, and truck-only lanes that provide convenient, exclusive freight access and minimize congestion and safety issues on local roads. The project is also one of the first to use concrete segmental construction and incorporate the new AASHTO Bridge Code.
Atkins' ability to mobilize staff in support of this project enabled completion of alternate bridge designs three months early in an aggressive design schedule. Aesthetics also played a key role in the project, with designers making every effort to incorporate the style and character of historic Ybor City. One of the project’s notable features is a “gateway” that evokes the area’s unique, century-old Florida architecture. The project received the Florida Institute of Consulting Engineers (FICE)/FDOT 2014 Outstanding Project Award, FICE 2015 Engineering Excellence Award, American Council of Engineering Companies (ACEC) 2015 National Recognition Award, and American Segmental Bridge Institute (ASBI) 2015 Bridge Award of Excellence (urban bridges category). The Colorado Department of Transportation (CDOT) selected Atkins to help address the immediate need to improve safety and congestion that has plagued this corridor for many years. The Twin Tunnels project widens the lanes of I-70 from Idaho Springs to the base of Floyd Hill and is the first project to add capacity to the corridor in over 20 years.
After successfully assisting with the concept design in an environmental assessment, CDOT selected Atkins to complete the eastbound tunnel expansion project under a construction management/general contractor delivery system. After the completion of the initial eastbound tunnel, CDOT sole sourced the Atkins team to complete the westbound tunnel. The compressed delivery schedule and complexity of the project required tapping into Atkins’ worldwide expertise in tunnel design, managed lanes, bridge and retaining wall design, highway design, and construction phasing. The team developed creative solutions to maintain traffic flow during construction, mitigate environmental impacts, and increase highway safety and operations.
The project was named Engineering News-Record (ENR) Mountain States 2016 Best Project in the highways and bridges category (Colorado, Wyoming and plains states). The A3 bypass at Hindhead was constructed to improve road safety, reduce congestion and improve air quality.
Running beneath Devil's Punch Bowl, a site of Special Scientific Interest, the new dual carriageway includes the longest non-estuary underpass in the UK – 1.83km of twin bored tunnels. With traffic congestion now absent, the existing road south has been downgraded to a local distributor road, while the northern carriageway has been closed and restored to heathland, as it was a century ago.
The Highways Agency commissioned Atkins for design, geotechnical advice, site supervision, tender and contract documentation, noise and air quality assessments, and expert witness services. The railway alignment is designed to meet peak operational frequency of 24 trains per hour. The Central London tunnels are 6.2m internal diameter constructed by Tunnel Boring Machine and lined with Precast Concrete Segmental rings. Tapered tunnel rings, with 8 segments are designed to accommodate the minimum track alignment radius. The majority of the tunnel segments are steel fibre reinforced and include poly-propylene fibre for fire protection. Segment joints are designed with locating dowels to facilitate high quality build ensuring good waterproofing performance and long term durability of the tunnels environment.
Curved geometry on the segment joints is included to improve performance and protect the segment. There are a total of 18 cross passages along the bored tunnels length constructed in a variety of linings, including; insitu concrete, pre cast SGI and sprayed concrete. Openings in the running tunnels to the cross passages were provided using hybrid PCC / SGI opening sets or steel reinforced PCC rings. There are 3 bored tunnelling contracts, C300 West, C305 Central, C310 East. A 4th tunnel contract, C315, connects the central and eastern tunnels via the refurbished Connaught brick lined tunnel that runs under the Royal Dock in East London. The C300 western tunnels were driven through the heart of central London from Paddington to Farringdon running directly under Oxford street using Earth Pressure TBMs.
The PCC running tunnels were driven in advance of the stations being constructed. TBM station alignments were developed together with temporary segments to provide pilot tunnels from which the large diameter SCL platform tunnels were then constructed. On Contract C305 the tunnels pass beneath the two major financial districts; the City of London and Canary Wharf. Tunnelling was undertaken by EPB TBMs and faced some of the most challenging conditions where water bearing sand lenses were encountered. The TBMs were driven in parallel with station constructions which required TBM arrival, transit and re-launch systems to be developed. Contract C310 tunnels were constructed through Chalk with slurry TBMs to control water ingress. All the central London tunnels will be connected by the first quarter of 2015, with Crossrail scheduled to be fully operational by 2018.
Alila Jabal Akhdar is a boutique hotel consisting of 86 suites, a spa, meeting facilities, restaurants and all related support facilities. It is set to be an exceptional addition to the high-end tourist destinations in the Gulf region, and a catalyst for further developments in this stunning part of Oman. Sustainability was a strong driver for the project’s architects and engineers. In order to maximise the use of local materials and reduce the energy footprint, the development is designed to make the best use of carbon critical principles and to achieve Leadership in Energy and Environmental Design (LEED) certification. The project has demonstrated industry best practices in line with LEED principles, some of which include: • use of local rocks retrieved during excavation for the stone masonry; • international standards of recycling practice; • minimisation of disturbance to the existing natural landscape, flora and fauna, and to local people living in the vicinity; • water conservation practices, including use of curing compound to mitigate the scarcity of water; • management of robust processes to identify and mitigate risks.
The development’s landscape design is focused on minimising the use of water through a selection of gravels, paving and a palette of plant species accustomed to the Jabal Akhdar climate and soil conditions. The site is located in Chengdu along a river bank and surrounded by Hotel tower and adjacent residential development. The Landscape concept takes reference from the typical natural mountainous Chengdu landscape., which is known to be very humid and contains dominant bamboo vegetation.
The Hotel landscape is themed as “Mystic Landscape “ which shall become a signature landscape feature and reinforce the strong iconic identity of the Hotel development. Selection of native plants are further enhancing the Chengdu reference and Gingko trees are used throughout. Form and color of the local Ginkgo tree” is also adopted ias a design inspiration for various hardscape features such as planters, paving and water features. Natural dynamics such as wind and sound are introduced throughout an artificial mist pond and plantations of Bamboo along the river bank.
Aberdeen, the largest satellite town of Hong Kong city, is a vibrant waterfront harbour resort. It is unique in the sense that it puts forward the traditional lifestyle and modernity on a single platter. Floating restaurants and sampan rides are highly acclaimed features of this tourist centre, which is one of Hong Kong’s oldest and most popular tour attractions. Visitors can cruise around the fishing port on a boat once boarding at the newly designed sampan piers. The uplifting works along Aberdeen and Ap Lei Chau aimed to preserve the features of a fishing port. In view of the distinct characteristics of Aberdeen and Ap Lei Chau, apart from the functional requirements of operating in a safe, environmental friendly and effective manner, the proposed works such as the repaving, soft and hard landscape, sculptures, display board and directional signs, kiosk, leisure and resting area, etc will be aesthetically pleasing and will become the iconic designs to reflect the theme of “Traditional Fishing Village” to blend in with the cultural and heritage nature of Aberdeen and Ap Lei Chau in harmony. Various landscape components along the promenade such as feature seating, performance stages or pavilions, make reference to traditional artifacts and lifestyle.
Lush planting with different textures have been carefully chosen and introduced along the promenade as soft landscape and form the pedestrian green walkway. People who have passed most of their life on dry lands would find fishing life of Aberdeen very intriguing as conventional lifestyle still prevails in Aberdeen. The Hainan Wanning Jun waterfront residential area is the key seaside resort of CITIC Group; this development’s area is very big so that it have to be developed phase by phase; Atkins landscape and architectural design team participate in the design to provide professional knowledge and perspective, together with client to create a modern upscale resort district. Trying to create the southeast landscape environment through introduction of palm trees, features sculptures, the pool of free boundary and diverse Southeast Asian vegetation. The combination of varies of elements, such as the organic arrangement, integrated layout, connection in-between architecture and landscape, the spatial variation, visual connection, all these have been set accordingly with the project.
Atkins' East Lake design connects the old and new areas of Karamay through a distinctive landscape, building on the tradition of water festivals whilst introducing and enhancing ecological provision unique to Xinjiang. The design takes inspiration from Karamay’s natural and historical heritage, with particular reference to the cities importance as an oil reserve. Building on Karamay’s history Atkins’ proposal looks to protect and enhance the local biodiversity whilst providing an attractive destination not only for locals but tourists also. Atkins’ idea was to offset any new built form with an area for nature, so Incorporating a landmark bridge with new lake islands, recreational piers with functional wetlands; all contributing to the ideal of ‘city living’ in harmony with nature.
According to “Mountain and Water” from Chinese culture, Atkins designed the following nine items: a central lake, leisure and fitness area, resort, adventure park, cultural display area, lakeside business, Northern Xinjiang Garden, entrance plaza and wetlands. “The benevolent enjoy mountains; the wise enjoy water”. The M25 is the busiest road in the UK and strategically important to the economy. Atkins is part of the including, and Egis Road Operation UK which was appointed by the UK’s Highways Agency in 2009 to manage the M25 and its key arterial link roads.
As part of this 30-year contract to manage and enhance London’s orbital motorway network, we are delivering lifecycle maintenance and major improvement projects. These include widening 38 miles of the M25, refurbishing tunnels and bridges, delivering Smart Motorways with all lane running and installing hundreds of variable messaging signs and gantries, helping to maximise the use of the network and deliver more reliable journeys. We also manage the Dartford River crossing, and operate and maintain 440km of this economically strategic road network providing our customer and road user with a world-class highway service.
Delivering the first significant widening programme before the London 2012 Olympic Games was a huge challenge, and to meet the deadline the design and construction had to be twice as fast as previous comparable projects, expending around £1 million per day and widening the motorway at a rate of 1.6km/month. The second phase of widening includes the transition to all-lane running. Section 5a (Junctions 23-25) and Section 2 (Junctions 5-7) went live in April 2014. The contract transfers the investment risk in lifecycle maintenance to the Joint Venture for 30 years and requires us to meet challenging performance requirements.
Atkins is involved in all aspects of maintenance scheme delivery, from data gathering and inspections, through solution evaluation and whole life costing to detailed design and management of activities on the network. Some 200 individual schemes are progressed in any 12 month period and as such works must minimise road user impacts. This has driven innovation in many areas for example; solutions for concrete pavement repairs, major bridge joint renewal and bridge deck waterproofing replacement. Part of the Trans-European Road Network, the M62 Smart Motorway scheme is of strategic importance on a regional, national and international scale. Atkins developed an innovative design for this project to provide 15.5 miles of extra road capacity to reduce congestion and provide safer journeys for motorists. The design includes the use of Dynamic Hardshoulder Running and All Lane Running (ALR), where the existing hard shoulder is converted into a running lane.
This is the first scheme in the UK to implement ALR and this approach delivered savings of around £3 million as less technology was required. To deliver this scheme two months ahead of schedule and under budget, our design team worked collaboratively with main contractor BAM Nuttall/Morgan Sindall Joint Venture (bmJV) and client, the Highways Agency. Innovation was key to successful delivery such as 3D modelling, developed by Atkins. These models informed the design process so well and achieved early buy in from stakeholders to new layouts that it led to a reduction in infrastructure requirements, saving the project £9 million. The 3D models were able to replicate views from properties allowing impacts to be determined and minimised as well as facilitating early engagement with residents to agree mitigation measures if required. The models were also able to replicate CCTV camera images ensuring full coverage of the scheme and also meant that cameras were positioned in the right place, first time.
Atkins’ design team were also behind the introduction of 19 metre span cantilever sign/signal gantries, the longest to be installed on the network. These cantilever gantries reduced costs and minimised the impact on the local environment including visual intrusion to local residents. Officially opened in September 2013, the scheme has seen around 15 minutes taken off the average journey for all road users. Atkins has been commissioned by the Widus Hotel & Casino, the premier leisure destination in Clark Freeport Zone, Philippines, to provide masterplan and full scope architectural design services for a major expansion of the property.
Upon completion, the integrated resort destination will cover an area of 170,000sqm - approximately 4 times its current size. The design’s ambition is to create a fully integrated resort that will be a landmark design in Clark. The wide variety of entertainment, gaming, shopping and dining facilities will ensure the development is popular destination for all who visit. Guests arrive by car or bus under a dramatic smoothly contoured cantilevered roof that covers the main drop-off and entrance. Fountains and dramatic lighting will enhance the visitors experience further from where they enter the sky-lit main entrance hall. Beyond the entrance hall is the main gaming area located at the heart of the integrated resort. The gaming area can be accessed by guests from multiple directions coming from the drop-off, the existing hotels and the new retail areas.
The main gaming area is conceived as a grand space designed to be as flexible as possible with 36 metre clear spans between columns. From the main entrance visitors can then easily access a spectacular new hotel guest lobby with its three-storey high tree filled atrium as well as the Korean themed shopping mall, food and beverage area and entertainment facilities. Extensive VIP gaming areas and private VIP gaming rooms are provided on the main level and also on the upper public level that overlooks the hotel lobby atrium.
The 80m high new hotel tower of the development accommodates 250 guestrooms on the lower floors and 100 VIP suites on the upper floors. The VIP suites are complimented with VIP lounge, dining areas and terraces. The extensive glass facades of the tower guarantee excellent views of the hills, mountains and golf courses around Clark. Hotel guests are able to use the extensive gardens and swimming pools located on the top level of the podium deck that includes an infinity edge swimming pool orientated towards the Zambales mountains to the west of Clark.
From the pool deck area guests can walk down to the new waterpark that is for exclusive use of the guests staying in the different hotels of the resort. The waterpark includes a wave pool, lazy river and a series of swimming pools and terraces that to provide a place of fun and relaxation for visitors and their families. Sustainability is a major focus of the development. The integrated resort in particular will set new standards in energy efficiency due to its careful orientation of the tower and the sophisticated design of facade sun shades. It is also intended that energy will be generated from the large array of photo-voltaic panels on the casino roof. Atkins provided full multidisciplinary design and management of the civil works on Dubai Metro.
This included geotechnical and site investigations, bored tunnels, viaducts and bridges, route alignment, depots and additional specialist services such as fire and ventilation, environmental impact, concrete durability, noise and vibration reduction and landscaping. The first line of the Dubai Metro opened to the public on 09 September 2009. It is the longest automated, driverless system in the world and it has eased traffic congestion by improving mobility throughout Dubai. A key challenge has been to integrate the specialist skills from Atkins' international offices to work with our local presence on this tightly programmed project. Another challenge was to tackle the project in a carbon-critical way.
Our approach resulted in less glass and more insulation than the original designs. Our recommendations saved just over 500m 3 of aluminium and a saving of approximately 12,900t (CO 2-e) and reduced estimated peak cooling load by around 35%. Northamptonshire County Council aims to be the first area in England with Superfast Next Generation Broadband by the end of 2017. A critical component of this project was effectively communicating the progress of the broadband service roll out to people living and working in Northamptonshire. To help Northamptonshire do this, Atkins developed the Superfast When & Where Portal which can be accessed online via. Traditionally maps like this would be in static paper or PDF format, so the interactive web map represents a new way of engaging with constituents. With the Portal accessible via desktop, mobile and tablet, people in Northamptonshire can search by postcode and see when they will receive superfast broadband at their home or business.
Since going live in November 2013, the Portal has been well-received by the public. Andrea Leadsom, MP for South Northamptonshire mentioned the site in a speech in the House of Commons, saying: “Northamptonshire County Council has one of the most detailed “when and where” maps in the country.” PC Pro magazine also cited the project as an example of fibre broadband coverage map best practice in their July edition feature on ‘Who’s getting fibre’. The P-17 Tower is a stunning, 77-storey mixed-use tower development which is set to grace Sheikh Zayed Road in the neighbourhood of Dubai International Financial Centre (DIFC).
The design of the super-slim P-17 Tower gives the illusion of constantly changing its appearance with the movement of people and the sun. Standing tall at 370 metres and just 30 metres wide, the tower’s darker front facade rises from the ground and twists slightly in a striking glass and steel design. Behind the elegant form, increasingly taller blades gently splay outwards, conveying the appearance of layered planes which dynamically move sideways to produce a challenging, gravity-defying form. The design integrates contemporary architectural thought, with innovative engineering solutions. At the mid-building level tower, an angled atrium cuts straight through the tower filling a void over several storeys, which serves the five-star hotel and the serviced apartments. Above the hotel are premium residential apartments and two floors of VIP suites which enjoy incomparable views of Dubai.
Our urban designers created a vision which will help grow and bring new vitality and vibrancy to the Downtown and Business Bay districts in the heart of Dubai. Our urban designers focused on the public realm – the space between buildings – to provide a solution which will deliver a true sense of place and identity, ensuring long-term environmental, social and economic resilience.
This vision has provided the platform for a new cultural centre which will be home to museums, art galleries and an Opera House, as well as the development of an 80 million sq ft precinct linking Downtown Dubai to Business Bay. Mohammad Bin Rashid City will be a major new mixed-use development comprising residences, hotels, retail outlets, commercial and community space. Our masterplan visioning provides a cohesive design at ground level which will improve connectivity and permeability for pedestrians and cyclists.
The waterfront will have a distinct character with green spaces along its frontage that integrate into public spaces, thus making it accessible to other areas of the development. Targeted development, both in terms of public space and individual buildings, will provide for a cohesive, carefully planned sustainable urban environment.
Atkins' work on the iconic 321m-high, 56-storey super-luxury hotel included architecture, civil and structural engineering, MEP engineering, construction supervision and cost consultancy services. The hotel is situated on a man-made island and is considered a symbol of modern Dubai. The Atkins-designed Burj Al Arab, with its distinctive theme of a billowing spinnaker sail of a high-tech J-class yacht, ranks alongside the instantaneously recognisable icons of other world cities. When it opened in time for the millennium celebrations, it was the world's tallest single structure hotel housing the world’s tallest atrium at 182m.
The masterplan for Baku White City aims to transform the area into a brand new, high quality urban quarter, acting as a catalyst for the regeneration of the city and the wider region. Atkins was asked to develop the long term strategy for the 220 hectare site, located on the eastern edge of Azerbaijan’s capital city. Our vision looks to achieve this through the creation of a cohesive, carefully planned sustainable urban environment, offering distinct character and a high quality of life for its residents.
It also presents an opportunity to attract and promote investment, generate jobs and strengthen the city’s economy. Atkins designed and provided construction supervision services for the 360m-high commercial tower, the centrepiece of the Jumeirah Lakes development and host to the Diamond Exchange facility.
Almas, meaning ‘diamond’ in Arabic, was Atkins' inspiration behind the distinctive projecting facets of the two-storey steel podium at the base of this 60-storey tower. Eight diamond facets reach out in total with the most prominent facet housing the actual Diamond Exchange, the largest of its kind in the Middle East, where stones can be viewed and traded. The podium glass is of a specification such that the diamond inspection process will not be influenced by the light. Al Habtoor City is a major mixed-use development alongside Dubai’s Sheikh Zayed Road. Atkins is working for Al Habtoor Group to provide full multidisciplinary design services for the residential element of the scheme, incorporating three luxury residential towers and a retail podium totalling 395,000 m².
The development will also include three five-star hotels and a spectacular water-themed theatre. Upon completion, the project’s location in Business Bay on the banks of the planned Dubai Water Canal will ensure it becomes a key destination for tourism and leisure. Atkins was appointed in 2011 as lead designer for the expansion of King Abdulaziz International Airport in Jeddah. The 36-month project involves designing a new 640,000 m² passenger terminal and associated buildings to increase the airport’s capacity to 30 million passengers each year.
In addition to lead design activities, we are undertaking the architectural, special airport systems (SAS) and information and communication technology (ICT) design for all aspects of the terminal building, including an advanced baggage handling system, departure gates and airway bridges, a 56-room hotel for transit passengers, four first class lounges and a business lounge and duty-free shops and commercial centres. The airport expansion is needed as Saudi Arabia seeks to meet demand from religious tourism to the holy city of Mecca. Approximately 2.5 million people visit Mecca during the Hajj period alone, and this is projected to rise to 4 million in the next few years.
Atkins provided masterplanning, architecture, landscaping, environment, transport, civil engineering and project management services for this sustainable residential, commercial and leisure resort community for a population of 60,000. Atkins' environmental considerations were central to the design, engineering and construction of the 13 offshore islands, golf course and marina. Alongside the design of the islands and the contours of the land to be reclaimed, we designed a number of features such as living areas, hotels, recreation zones, community facilities, transportation, water networks and power sources distribution.
Atkins has been appointed to a three-year contract by the Qatar Ministry of Municipality and Urban Planning to support delivery of its multi-billion dollar transport and infrastructure programmes underpinning Qatar’s 2030 vision for world class infrastructure development. Under the contract, Atkins is establishing a Central Planning Office (CPO) to co-ordinate current and planned road, rail, metro and other major transport and infrastructure projects, including elements associated with the FIFA 2022 World Cup. Qatar’s 2030 vision includes programmes for education, health, science and sport, all of which must be connected by multimodal transport infrastructure.
The CPO will be a single co-ordinating body which will be responsible for ensuring all works are planned in an integrated and efficient way to minimise disruption and maximise cost effectiveness. Atkins’ project team draws upon a wide range of skills from rail to tunnelling, traffic planning to environment, urban design to cost estimating. Atkins conducted an Environemental Impact Assessment at Barr Al Jissah to identify a coral community that could have been damaged. A decision was taken to transplant the suitable coral onto a man-made substrate in a location which would not be impacted by construction. A total of 41 small concrete forms were constructed with rough faces and a number of openings to allow coral and reef organisms to be transplanted. In total over 200 coral colonies were relocated with every attempt made to minimise disturbance and abrasion.
Atkins provided multidisciplinary services for the twin 240m high office towers and shopping mall of the Bahrain World Trade Center. Atkins achieved a world first by aesthetically incorporating commercial wind turbines into the fabric of the building. The three 29m diameter wind turbines and the shape of the paired towers have a direct and tangible relationship via wind dynamics.
The Carbon Critical Design of the Bahrain World Trade Center meant it was fully tenanted by major regional businesses from day one. Atkins also received a number of accolades for the design including a Best Tall Building award from The Council for Tall Buildings and Urban Habitat, a Construction Week award and an Innovation award from The Building Exchange. Atkins delivered the Signalling and Power and Distribution contracts for the CASR which have modernised life-expired signalling equipment across 192 route miles of track between Newport and Port Talbot. A technically challenging project, CASR was one of the first major signalling schemes in the UK to use latest innovations such as plug couplers and Frauscher train detection technology to help save time and money. Over the course of the scheme, the team undertook a range of tasks, including centralising control of signalling equipment to the Cardiff Control Centre, installing an electronic crossing controller system and providing an improved power and distribution system.
Completed in 2016, this project has provided more efficient and reliable passenger and freight services to meet demand in the South Wales region. The A380 is the largest passenger aircraft in the world with a wingspan of 80 metres. Atkins provided independent certification of the A380 wing structure to enable its client to comply with international air safety standards. Atkins’ A380 wingbox certification covered detailed stress analysis extending over the whole aircraft lifecycle, operating loads, in-service fatigue and damage tolerance. To deliver the project, which extended over four years, Atkins brought together a large team and managed inputs from a wider supply chain. The A380 has a ground-breaking, fuel efficient design, resulting in 12% lower fuel burn per seat than a comparable aircraft. To provide certification Atkins was required to develop new and innovative stress analysis methods.
Completed in 2012, we successfully delivered the detailed design for the upgrade, one of the UK’s most important and technically challenging rail modernisation programmes. Atkins helped develop the project from its infancy, right through to detailed design and final commissioning. Drawing on knowledge from across the company, over 400 engineers were involved in the project to deliver the multidisciplinary elements of the scheme. This included pway,, E&P, and, plus the associated,, and surveying. Atkins also undertook the installation, testing and commissioning works for the new signalling system.
Now finished, journey times have been reduced and there are more frequent commuter services on the line between Birmingham and London Marylebone. As a result of these improvements, passenger numbers increased by over 30 per cent in the 12 months after the works were completed. These programs include construction of new roadways, widening of existing roadways, construction of new bridges, replacement of existing bridges, roadway safety and operational improvements, intersection safety and operational improvements, resurfacing, and pedestrian and bicycle improvements.
Atkins has been selected five consecutive times as Program Manager, working side-by-side with and as an extension of county engineering staff. We serve as the representative to the board of county commissioners and field public inquiries related to construction projects. As a measure of Atkins’ dedication to responsiveness, our inspectors are routinely sent to resolve transportation issues and concerns of the local citizens. Through close coordination and partnership with the county’s department of transportation staff, we have consistently accelerated construction schedules and reduced construction costs to meet proposed budgets. We also provide input and assistance in the development of the future TIP as well as participating in associated public information programs. Our deep-rooted and long-term collaboration with Cobb County extends past our involvement on the project and participation in the Chamber of Commerce, where we work closely with the business community. Our team members are also actively involved in local charities that serve the community and initiatives that contribute to the County’s economic health.
An example is the annual Atkins Golf Tournament that benefits the Earl Smith Strand Theatre, a restored and treasured venue that anchors historic Marietta Square. Oxford Circus, in the heart of London, is one of the world’s most congested intersections, with more than 80 million pedestrians crossing it each year. The innovative makeover allows shoppers to walk across Oxford Circus diagonally for the first time.
Atkins' design was inspired by Tokyo's famous Shibuya crossing, renowned for allowing people to cross with ease. Atkins was appointed by the Crown Estate to improve pedestrian movement and the quality of the public realm. This involved the introduction of the UK’s first large scale, diagonal crossing and a radical increase in the amount of footway space. Our solution enabled all existing barriers and street clutter to be ripped out and remodelled in order to give pedestrians the freedom to move around quickly both straight ahead and diagonally – across both Regent Street and Oxford Street. To test such an innovative approach our transport planning team and our Intelligent Space pedestrian modellers initially developed computer models including 2D real time simulations for vehicles (VISSIM) and pedestrians (LEGION). The urban design team combined this data and prepared a 3D animated, photo-realistic environment (3D Studio Max model) with specialist Design Hive, which was used for stakeholder and public consultation.
A seven month programme of site operations had to coordinate with London Underground improvements, maintain safe and convenient retail operations, street clutter clearance and utilities works, as well as implement improvements including granite paving, lighting mounted on buildings and wayfinding. The completed project had drawn significant public and professional support and Oxford Circus is again a place to visit for its change in character both by day and by night. The solution has resulted in a dramatic reduction in pedestrian congestion. Atkins is part of the team delivering the £250 million - the first in the UK to be delivered as a ‘pure alliance’. To boost capacity and reliability on the West Coast Main Line, Atkins is working collaboratively with, and to deliver a package of improvements by 2017.
Works include linespeed improvements between Crewe and Norton Bridge (now complete) and the wholesale resignalling of Stafford and the surrounding area. Six miles of new railway will also be constructed at Norton Bridge including a flyover which will help to provide a faster more reliable railway. Once complete, the programme will deliver two extra fast trains per hour between London Euston and the North West, one additional train per hour between Manchester (Stone) and Birmingham and one additional freight path per hour through Stafford via Trent Valley, helping take lorries off congested roads such as the M6. By working as a pure alliance, the first of its kind in the UK rail industry, all partners share equal risk and reward. This means that the project will be delivered more effectively, with all parties working in a truly collaborative manner. This approach is the way forward for rail infrastructure delivery in the UK.
The Prince Sultan Cultural Center Company envisages a development which will engender “social wellness”, through which residents will take “an active part in improving the world by encouraging a healthy living environment and initiating better communications with those around them.” The masterplan for the project incorporates all the components needed for a strong community: residential; culture; healthcare; education; retail; offices and commercial space; exhibition and hospitality; and an integrated public realm network. The idea behind the project is to create a new type of community for the Kingdom of Saudi Arabia which encourages ownership and involvement from everyone in order to promote physical and mental wellbeing. Every element within the masterplan has to meet this wellness criteria in order to create a city within the city of Jeddah – a fully self-sustaining mixed-use development. The site area of approximately 2.4 million square metres features 40% high quality public realm comprising gardens, urban squares and shaded walkways all interconnected by a large central linear park.
Atkins is assisting Rail Net Denmark to deliver the most important combined upgrade in passenger and freight train services in Europe; the application of the European Rail Traffic Management System (ERTMS) across 3200km of twin track on the Danish rail network. The project promises a radical improvement in safety, performance and capacity, and opens up the possibility of running non-stop trains across all borders. The overall project consists of two large projects and two systems: the main and regional lines that will be equipped with ERTMS level 2 and the Copenhagen S-line, which will use CBTC (Communications Based Train Control). ERTMS will see on-board computers fitted to every train which receive and relay information via trackside radio beacons that communicate with a central control. This improves timetable reliability and offers capacity improvements as services can be run closer together.
Safety is also a key feature as ERTMS includes an Automatic Train Protection (ATP) system which applies a train's brakes automatically if there is danger of a potential collision. Atkins' teams of specialists are steering the project through all stages, which includes preparing tender documents for the supply of on-board train equipment and signalling infrastructure, technical assistance on client side and implementation of the systems. The programme is carried out by a Joint Venture consisting of Atkins, Ramboll, Parsons and Emch+Berger. Atkins is helping Bane NOR, the Norwegian railway infrastructure manager, deliver one of the largest current digitalisation projects in Norway: the complete resignalling of the Norwegian railway network. An integrated solution across infrastructure, rolling stock and traffic control will be developed. It will be based on the European Rail Traffic Management System (ERTMS), the European standard for automatic train protection, but will also include interlocking components based on national requirements.
ERTMS Level 2 (Baseline 3) has been chosen for the national rollout. This means that line-side optical signals will be removed and replaced by signalling on-board every trainset or locomotive. The entire Norwegian railway network, covering some 4,200 kilometres of railway tracks, will be equipped with ERTMS in a uniform fashion. More than 500 trains or other rail vehicles will be refitted with new on-board computers and other equipment enabling trains to operate both on ERTMS lines and on lines with legacy signalling systems. The new system will utilise a GSM-R radio network to provide continuous monitoring and full supervision of the position and speed of each individual train. All remaining manually controlled railway stations will get remote control and technical barriers to eliminate potential human error, improving safety on the railway network. Improved timetable reliability is also expected after the renewal, as a consequence of the higher availability of the infrastructure, full remote control and enhanced functionality in the new traffic management system.
Future capacity enhancements through increased automation will also be enabled by the new solution. The main ERTMS system contracts are expected to be signed in early 2018, and the upgrade to ERTMS functionality should be completed at the same time as planned new double-track intercity lines around Oslo are completed in 2034. Atkins is assisting Bane NOR with the direction and management of both the overall programme and several of the constituent projects. Atkins is the technical and procurement consultant for the 15.5km twin tunnel Copenhagen Metro CityRingen (City Circle Line) transportation system package which will transport passengers underground through the heart of the historic city. Together with a joint venture partner, Atkins is involved in the four critical stages of the project: concept design, tendering and procurement, evaluation and managing the delivery of this design, build, operation, and maintenance contract. Our international expertise, combined with our local knowledge and understanding of the existing metro system allowed us to identify and mitigate problems. The creation of a bespoke management tool was also used to trace requirements.
We have also recommended a train control system which will ensure greater safety and reliability while at the same time reduce the amount of equipment and maintenance required. When complete, this vital metro system will represent one of the most advanced transport systems in the world.
The ArRiyadh Development Authority (ADA) has proposed a long-term vision for the future planning of Riyadh, in which four urban sub-centres are to be created on the perimeter of the existing city. Riyadh East Sub Centreis to be the new centre for the eastern sector. As its name suggests, Riyadh East Sub Centre aspires to be a haven, providing shelter and relief to its inhabitants and developing a modern concept of urban life by providing vibrant, interesting spaces. It is dominated by a curvilinear, organically shaped public park that ties the north and south sides of the site together with a string of spatial experiences. These public spaces insinuate themselves into every aspect of the planning and use idealised aspects of Riyadh’s history, spirituality, culture, tradition, ecology and future aspirations as themes under an overall approach of sustainability.
The spaces within the park are.